Biomedical Engineering Reference
In-Depth Information
designed for applications where de
fi
brillation protection is desired, withstands pulses of up
to
s. At prices in the range $29 to $34 each (one patient connection), the
added protection provided by these fault interruptors is certainly a
5 kV for 10
ff
ordable for evaluation
prototypes, and sometimes even for the
fi
final design.
TESTING FOR COMPLIANCE
Although the presentation of medical device electrical safety standards above is by no
means intended to replace the actual standards in scope or in content, it hopefully intro-
duced many of the most important design requirements covered by the major standards.
With medical equipment, however, designing solely for compliance is not su
cient. The
consequences of a malfunctioning device can be so serious that testing to ensure proper
performance is of utmost importance. As such, construction standards are only one aspect
covered by applicable safety standards. The other major aspect de
fi
ned by the standards
comprises performance requirements.
Within this second category, standards specify the multiple tests which are applicable
to diverse types of equipment and to identify in detail the criteria for compliance. In fact,
almost every construction requirement is linked to a certain performance requirement
which de
nes the testing that is performed to verify the acceptability of the construction.
In essence, the electrical tests described by the standards are designed to probe insulation,
components, and constructional features which could lead to a safety hazard under either
normal or single-fault conditions.
fi
Ground Integrity
Since the enclosure of the medical device is the
fi
first barrier of protection against the risks
of electrical shock, the
first test to be conducted is one to assess the integrity of the pro-
tective ground which guards a metallic enclosure and any other grounded exposed part. UL
standard 2601-1 establishes that the impedance between the protective ground pin in the
power plug and each accessible part which could become live in case the basic insulation
failed should be less than 0.1
fi
. The standard also requires that the test be conducted by
applying a 50- or 60-Hz ac current with an RMS value of 10 to 25 A for 5 seconds. Despite
this, however, a reasonable approximation of this measurement can be obtained by using
the 1-A dc current supplied by the circuit of Figure 3.21. Resistance is then assessed by
measuring the voltage across the grounding path.
Here, op-amp IC2 and power FET Q1 form a voltage-to-current converter that is driven
by a reference voltage set by R6 to maintain a 1-A constant current on a conductor con-
nected between the ground terminal of J5 and connector J4. Power for the circuit is derived
from three alkaline D cells, providing a maximum voltage compliance of approximately
4.5 V. Because full-range operation of the circuit is accomplished by driving the gate of
Q1 well above its source-to-drain voltage, IC2 is operated from 12 V generated by charge
pump IC1.
You may notice that J2 and J3 are labeled to be connected to a
Kelvin probe
. This type
of test probe separates the point through which current is introduced from that through
which the voltage across the unknown resistance is measured. The use of such a technique
is required for low-resistance measurements because it e
ectively excludes the resistance
of the test leads and avoids the voltage measurement errors that are often introduced
by high-current-density concentrations on the current-injection terminals. As shown in
Figure 3.22, a large alligator clip (e.g., Radio Shack 270-344) can easily be converted into
a Kelvin probe by replacing the standard metallic axis by a nylon bolt with nylon spacers
to isolate the jaws from each other and by covering the ends of the inner spring with a
ff
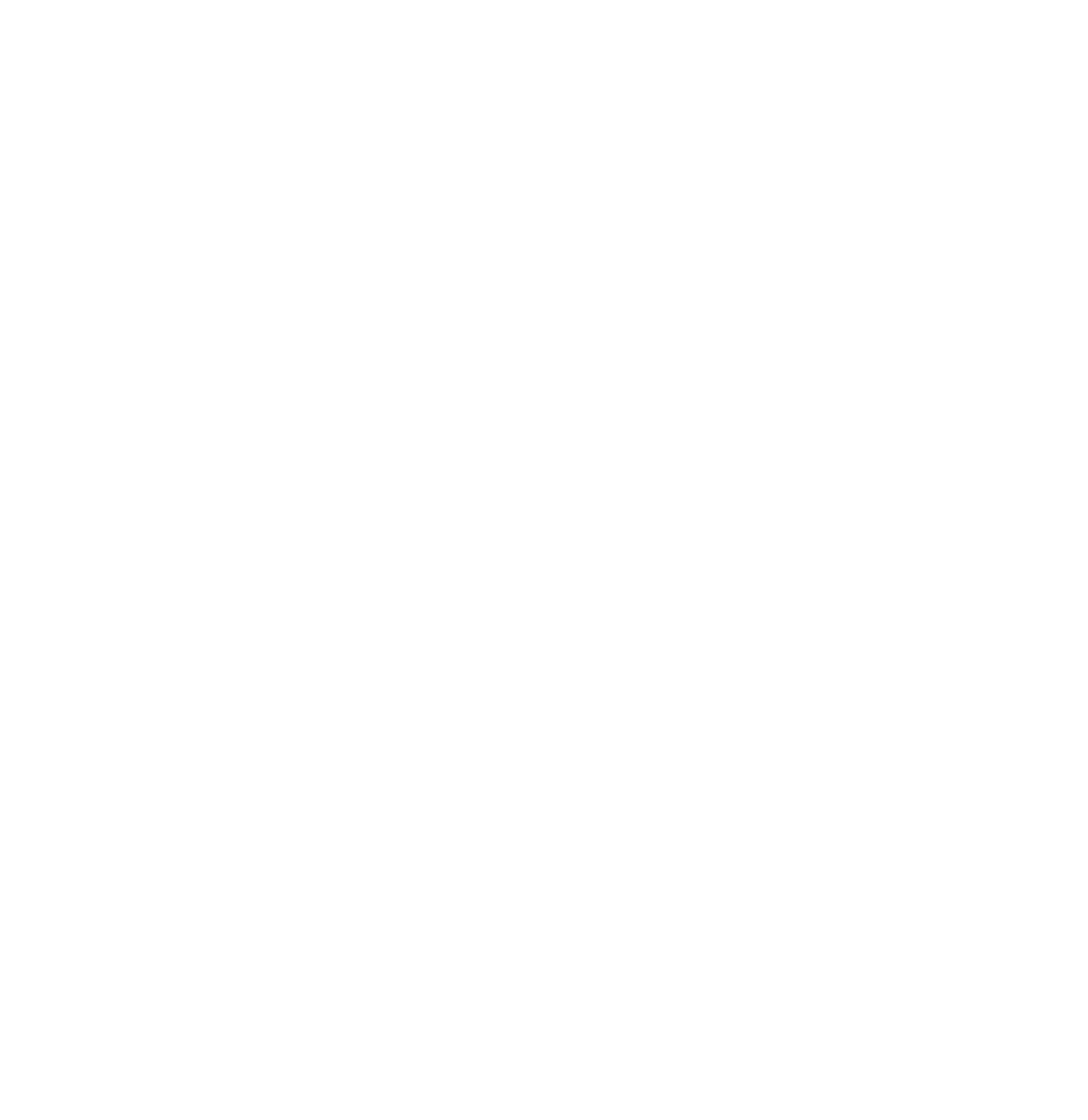
Search WWH ::

Custom Search