Biomedical Engineering Reference
In-Depth Information
illumination
mask
positive resist
negative resist
resist exposure
after resist developing
substrate
thin film to be processed later (for instance, etched)
Fig. 1.17
The optical lithography process
If necessary, the lithographical process is repeated several times using various
resists and masks, which need to be aligned at each step, the procedure being
accompanied by etching and deposition processes in a prescribed order to obtain the
final nanodevice or integrated circuit. The principal parameters of the lithographical
system are resolution and mask alignment (interlevel alignment values).
The resist materials are generally polymers, such as diazonaphthoquinone (DNQ)
or (poly)methylmethacrylate (PMMA) in the optical lithography case, the resist type
being a function of the illumination source (particle beams, optical, X-ray). The
exposure of the resist is performed in a direct write mode, when it is illuminated
point-by-point, through a mask, which is fully exposed, and the pattern is imprinted
in the resist by contact or proximity alignment of the resist surface to the mask (see
Fig.
1.17
), or by projecting the image of the mask. The mask is in direct contact
with the resist in the contact exposure method, which assures a good resolution
but damages the mask in the process, while in the proximity method, the mask is
situated at a distance d
mr
from the resist, which determines the minimum feature
size:
w
min
.d
mr
/
1=2
:
(1.22)
In (
1.22
), denotes the wavelength of the illumination source. In the proximity
method, d
mr
must be very small to obtain printed feature sizes the same as that
on the mask, which is a challenge in nanotechnologies. Therefore, the projection
exposure method is the most widespread high-resolution procedure in nanolithogra-
phy. In this method, an optical system projects the image of the mask on the resist,
improving the best resolution, which is given by
R
D
ˇ=NA;
(1.28)















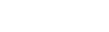
















Search WWH ::

Custom Search