Information Technology Reference
In-Depth Information
4
Tool Wear Analysis
In general pinion and ring gear are manufactured by using cutter heads which are
equipped with stick-type blades. Here the face-milling process, as described by [5] is
used for manufacturing. The plunging process is mostly used for the manufacturing of
the ring gear whereas the generating process is used for pinion manufacturing. Fol-
lowing different examples regarding tool wear of stick type blades in industrial appli-
cation will be presented. Here the tool wear behavior in plunging and generating
process with different tool concepts is compared to the new characteristic value K
G
. In
this report the focus is set on the discontinuous face milling process with carbide tools
in dry cutting.
4.1
Tool Wear Analysis of Plunging Process
In figure 10 the tool wear of two full profile blades is presented. They are used for
plunging process 1 and 2 where the ring gear manufacturing is realized. In process 1 a
cutting velocity of v
c
= 200 m/min and a ramp with a feed of f
BG
= 0.15 - 0.06 mm
per blade group was used. The cutter head with an outer diameter D
a
= 231 mm was
equipped with 7 carbide tools. The characteristic value K
G
was displayed in the dia-
gram over the unrolled cutting edge length l
s
which is separated into the outside blade
(OB), the tip area (T) and the inside blade (IB). The maximum tool wear occurs at the
corner radius of the outside blade (OB) to the tip area (T). In the simulation the cha-
racteristic value K
G
has its maximum at the same tool area. Additional tool wear oc-
curs at the corner radius of the inside blade (IB) and the tip area (T). In this area the
tool wear is less than at the other corner radius. The same tendencies are calculated in
the simulation. Thus, the good correlation of the calculated value K
G
and the real tool
wear is evident. On the one hand the maximum tool wear can be located by K
G
, on the
other hand the lower tool wear at the inside blade can also be calculated.
Ring Gear
Manufacturing (Process 1)
Ring Gear
Manufacturing (Process 2)
Full Profile Blade
Full Profile Blade
100
15
50
7.5
0
0
OB
T
IB
OB
T
IB
T
rake face
3 mm
3 mm
Fig. 10.
Tool wear analysis of full profile blades
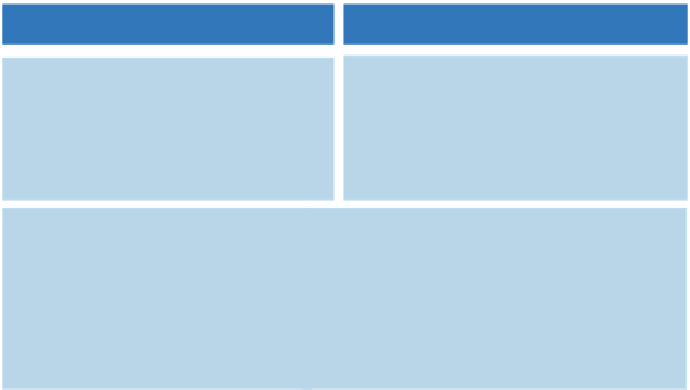
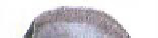

























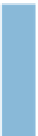
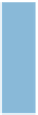














Search WWH ::

Custom Search