Information Technology Reference
In-Depth Information
3.2
New Approaches of Characteristic Values for Tool Wear Prediction
Within the investigations of [8] regarding tool wear in bevel gear cutting, it turned out
that especially the corner radius is critical regarding tool wear like chipping. This is
caused by the multi-flank chip-formation at the corner radius. Here the material of the
chip is compressed and squeezed, see figure 8. Thus, a simple analysis of the chip
thickness in this area of the tool is not sufficient.
From the figure it becomes clear that the chip thickness h
cu
is varying along the
cutting edge l
s
. Especially in the transition area of the corner radius between the flank
(IB) and the tip (T) a gradient of the chip thickness Δh
cu
/Δl
s
is visible.
The spatial compression of the chip is determined by the pressure angle of the tool,
as [11] presented. In order to consider the compression and squeezing of the chip in
the geometrical penetration calculation the gradient of the chip thickness can be used.
The gradient represents the varying chip thickness along the cutting edge l
s
. At the
tool flank the gradient is zero due to the invariant chip thickness. This is plausible,
because of the not existing compression of the chip material referred to the rake face
respectively the working reference plane, see [10].
Characteristic Values for Chip Compression
Gradient of Chip Thickness
Δ
Gradient of Working Rake Angle
Δγ
e
/
h
cu,m
/
Δ
l
s
Δ
l
s
Working Reference Plane
Working Cutter Plane
-
γ
e
compression of
chip
tool
chip flow
+
γ
e
chip
h
cu,m
l
s
rake face
workpiece
Δ
l
s
Δ
h
Δ
Δγ
Δ
cu,
l
m
e
Δγ
e
Δ
h
cu,m
l
s
s
Δ
l
s
T
IB
OB
T
IB
cuttin edge length l
s
cutting edge length l
s
Fig. 8.
Description of mechanical and thermal load due to the chip compression by geometrical
characteristics
A higher compression of the chip results in a higher thermal and mechanical load
at the cutting edge and the risk of tool wear. Due to the spatial chip formation and
compression a consideration of only the working reference plane is not sufficient.
Even the working cutter plane in which the chip flows orthogonal to the rake face has
to be considered according to DIN 6581 [10]. Both planes take the working direction
of the cutter into account. For the description of the chip compression in the working
cutter plane the gradient of working rake angle Δγ
e
/Δl
s
can be used, see figure 8. This
characteristic value represents the varying rake angle along the cutting edge and thus
the varying chip formation and compression. A rapidly changing gradient in a small
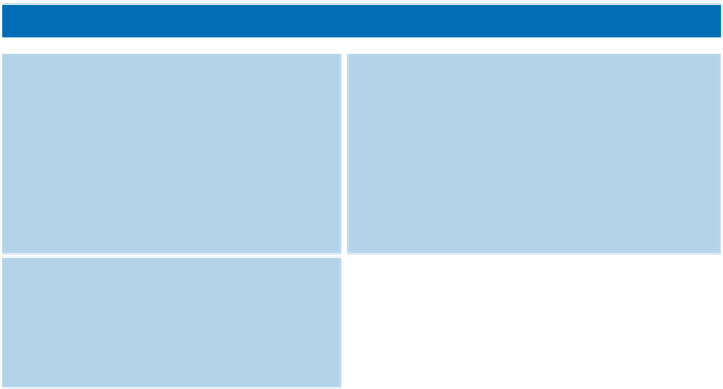

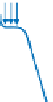






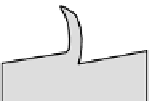



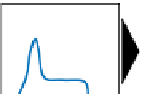


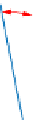
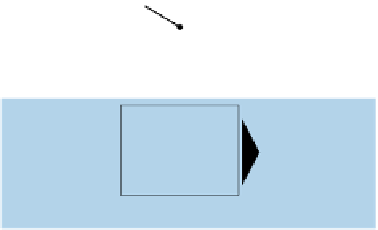
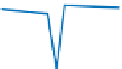

















Search WWH ::

Custom Search