Information Technology Reference
In-Depth Information
4
Surrogate Modeling and Optimization
In this section, a generic surrogate-based optimization scheme exploited here, as well
as the methodology for creating a surrogate model, is described. The specific method
utilized to align the responses of the low- and high-fidelity model, both the hull pres-
sure and skin friction distributions, is a multiplicative response correction.
4.1
Surrogate-Based Optimization Scheme
Our design task is formulated as a nonlinear minimization problem of the form
*
(6)
x
=
arg min
f
(
x
)
lxu
≤≤
where
f
(
x
) is the objective function,
x
is the design variable vector, whereas
l
and
u
are the lower and upper bounds, respectively. The high-fidelity model evaluation is
CPU-intensive so that solving the problem (6) directly, by plugging in the high-
fidelity model into the optimization loop, may be impractical. Instead, we exploit
surrogate-based optimization (SBO) [14,15] that shifts the optimization burden into
the computationally cheap surrogate, and, thus, allows us to solve (6) at a low compu-
tational cost.
The generic SBO optimization scheme is the following
(1)
i
+
()
i
x
x
=
arg min
s
(
)
(7)
x
where
x
(
i
)
,
i
= 0, 1, ..., is a sequence of approximate solutions to (6), whereas
s
(
i
)
is the
surrogate model at iteration
i
. If the surrogate model is sufficiently good representa-
tion of the high-fidelity model
f
, the number of iterations required to find a satisfacto-
ry design is small [27].
Fig. 7.
Edge of an element on the hull surface at radius
r
. The element length is Δ
x
and it makes
an angle θ to the
x
-axis. Pressure
p
acts normal to the hull surface. Shear stress τ acts parallel to
the surface.

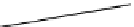





































Search WWH ::

Custom Search