Agriculture Reference
In-Depth Information
the bricks square prior to cutting to profile and for truing work. Each side was
equipped with, upon the bricks to be cut-molded were first rubbed flat on bed
and then stretcher and header faces rubbed to be at 90 degrees to the bed and
one another. Two benches, or 'bankers' large enough for both executing carv-
ing work and for the setting out, scribing and then checking the final accuracy
of the cut-molded brick shapes on the 'bedding slate'. Each banker was also
equipped with two specially shaped timber 'chopping blocks to hold the brick
in a reclined angle on a right-angled seating' to allow for carving header and
stretcher shapes, as well as the templets required for the various shapes. A total
of 110 templets were made for all the cut and rubbed moldings (Fig. 54).
Figure 54
Various templets
prepared from a full
size drawing. (Courtesy
of Price Masonry)
The templets were taken from full-size drawings of the architectural feature
drawn by the architects and the apprentices made each templet of a gauged sheet
metal on site. Following a pattern obtained from the iron brick axe we used to
cut and dress the moldings in England, I had brick axes made by a blacksmith
in Lexington, Virginia. One issue that had to be dealt with was the hardness and
strength of the brick. Although the bricks were made in a traditional manner they
were much harder than the traditional rubbing brick that we had worked with
whilst in England. Therefore in the carving of these shapes, traditional stone-
masonry techniques were also incorporated. Two Stonemasons, Andrew Bradley
from the National Trust's Culzean Castle and Graham Campbell of Historic
Scotland's Elgin Training Centre, whom I trained with on my Quinque fellow-
ship, were of great help in dealing with the differences in the brick. Gerard had
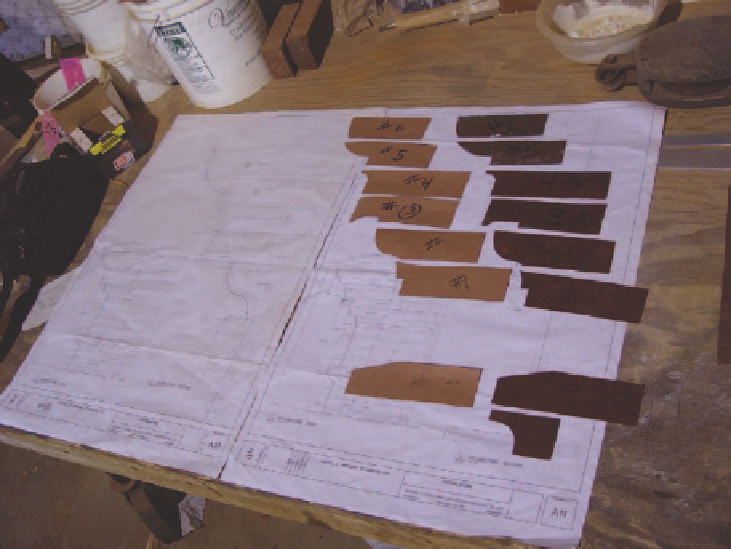