Biology Reference
In-Depth Information
bulk microcomponents to move across the substrate, directing
microcomponents to fall into receptor wells by shape recognition
and gravity force. Once in microwells, the components will be held
in place by capillary force. Usually, yet stronger connection will be
needed to provide permanent adherence. This is accomplished by
postprocessing steps, such as heating.
We have realized self-assembly of micro silicon circuit
components onto plastic substrates using this approach [9]. As
shown in Fig. 12.11A, receptor wells were formed on the plastic
substrate with lithographically patterned thick SU8, an epoxy-based
negative photoresist. At the bottom of these receptor wells, electrical
terminals were coated with a low melting point alloy. Correspondingly,
interconnect pads on freestanding silicon microcomponents were
patterned Au/Cr areas with high melting capability. In a hot and
acidic aqueous environment, microcomponents slid on the tilted
substrate and fell into receptor wells, as shown in Fig. 12.11B, and
then the microcomponents were anchored when their interconnect
Au/Cr pads contacted melting solder droplets in the wells.
Figure 12.11
Self-assembly process combining shape recognition, capillary
force, and gravitational force together. (a) The detailed
process of a single component. (b) The heterogeneous self-
assembly process. Reprinted from Ref. [9]. Copyright 2006
National Academy of Sciences, USA.
12.3.2
Microscale 2D Self-Assembly on Template
Involving Low Melting Point Alloys
In order to remove the need for any postprocessing, our group has
reported the use of low melting point alloys to assemble different

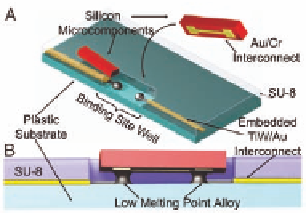
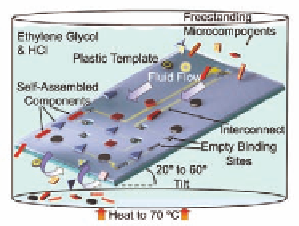
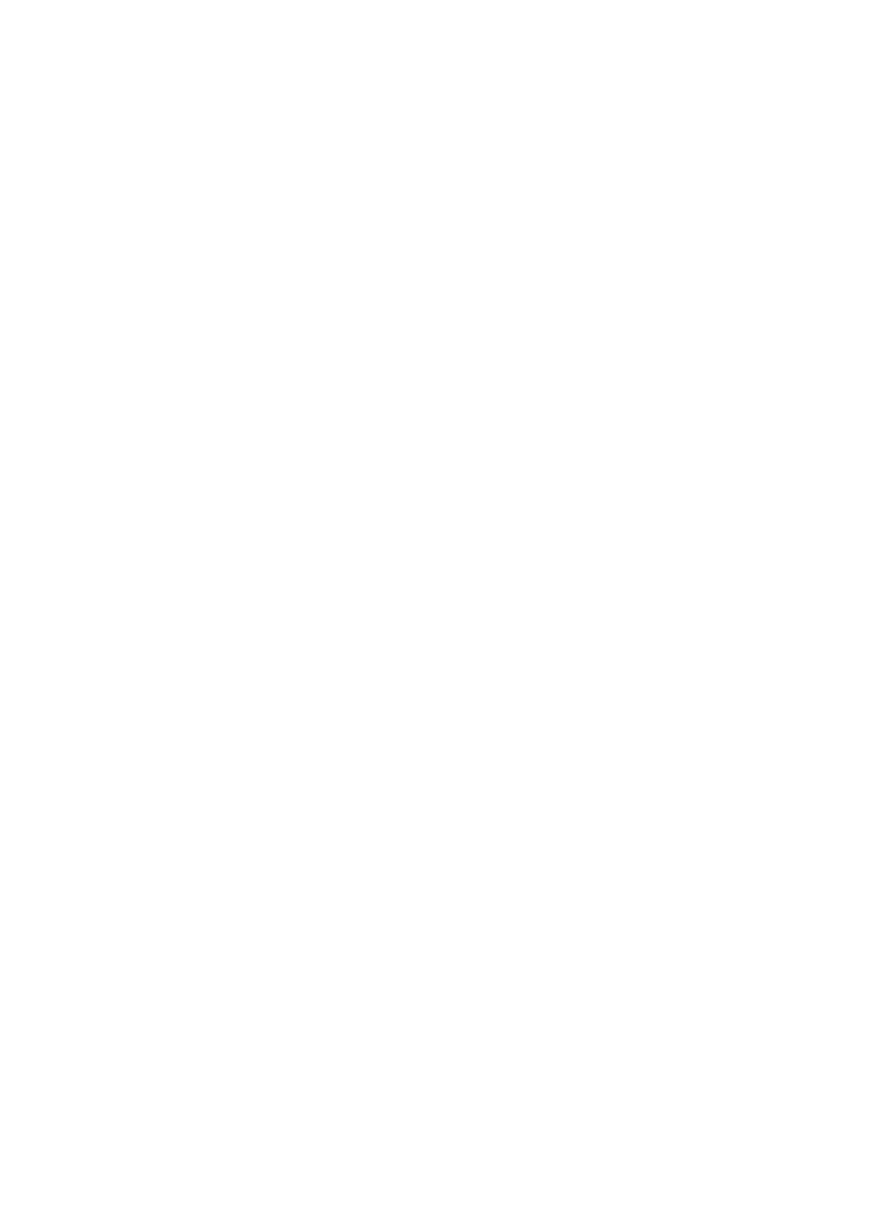
Search WWH ::

Custom Search