Geology Reference
In-Depth Information
The gravity flow method has apparently been tried on waste banks by excavating a reservoir on the top of
the bank and allowing H
2
O to flow naturally downward (Bruhn and Michalski, 1989). The constraint on
either of these methods is that the H
2
O is not uniformly distributed. It may flow through channels and may
bypass the fire zone. Even if the H
2
O fails to cool a small amount of material, the probability of reignition is
high.
Flushing is designed to fill the voids in an underground fire zone with fine, noncombustible solids. The
noncombustible material is intended to cover the burning material and fill the interstices in adjacent rock, limiting
the amount of oxygen in the system and absorbing heat. The high percentage of incombustible material, if properly
emplaced, is expected to form a barrier to further propagation of the fire. Flushing can be effective where
deposition of the noncombustible material can be controlled, where the voids have a relatively simple geometry,
and where the injected material will remain in place.
Sand, silt, red dog, crushed limestone, and fly ash are the most commonly injected materials. Air or H
2
Ois
usually used to carry the material through a borehole into the mine. With pneumatic (air) flushing, the
noncombustible material is deposited at the bottom of the borehole. It forms a conical pile that theoretically
reaches to the roof of the mine. Material is pumped into the hole to rejection, when it is assumed that the
void is filled.
Pneumatic injection has two constraints: the material does not penetrate rubbleized strata and the material tends to
slump which reduces the contact with overlying strata (Figure 1.2.6). This allows air to flow near the roof. In
hydraulic flushing, H
2
O is used to produce a slurry of the incombustible material. When the material is emplaced in
the mine, the solids settle as the H
2
O drains down dip. This method is believed to carry material further than dry
flushing and to have some penetration through rubbleized material.
Grout slurries have been pumped underground to form fire control barriers. Cement in the grout slurry
solidifies to form a competent seal, which also adds support to collapsed strata. The addition of foaming
agents and incombustible materials, like sand or soil, has been used to produce a lower density foam grout
that hardens to a cellular concrete (Colaizzi, 2004). The grout encapsulates the burning coal and limits
combustion by limiting exposure to oxygen. The foamed grout has a low thermal conductivity, between 80
and 228 cal/min/m
2
/°C/cm and acts as an insulator, retaining heat within the coal. To remove heat, a thermal
aggregate like small metal particles can be added to the grout (Terry, 1987). To be effective, the remotely
emplaced grout seal must be complete, encapsulating all burning material and isolating it from other
combustible materials (Figure 1.2.7), and the grout barrier must be stable for extended periods of time
while the material cools.
Borehole
Roof coals
Mine
Voids
During
injection
Injected
noncombustibles
Pneumatic flushing
Roof coals
Airflow
After
injection
Noncombustibles
Figure 1.2.6. Sketch of pneumatic injection through boreholes, allowing slump of injected material and continued
airflow near roof coals. From Kim and Chaiken 1993, p. 36.
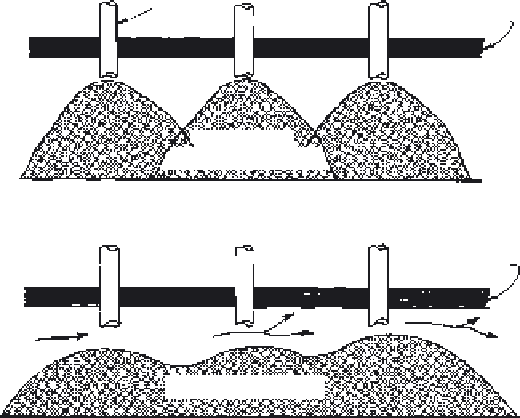