Biomedical Engineering Reference
In-Depth Information
cell cultures. In filtration systems a few circular disks are designed below
the rotating cone. This way, due to the fact that shear force, pressure gen-
eration, and the specific hydrodynamics of the system are decoupled, shear
rates can be easily optimized and precisely controlled to maximize filtration
performance while viability of the shear sensitive animal cells is maintained
(Vogel et al. 2002).
So far two different categories of devices have been suggested for uniform-
ing the bottom shear stresses. The first one is suggested by Gust (1990), and
is composed of a rotating disk in a cylindrical housing. Through the central
section of the disk fluid is pumped out and is reentered into the container via
the peripheral zone. The disk has optional skirts attached to it (see top image
in Figure 10.2).
In the second category, the rotating disk has a conical shape (either flat
or curved), and is suggested by Kroner and Vogel (2001) and in modified
versions by Sun and Lee (2005) and Ting and Chen (2008). The geometrical
configuration of the second category device—termed as shear inducer—has
been shown in the middle image in Figure 10.2.
As shown by Khalili et al. (2008), the shear stress uniformity generated by
microcosms covers only 72% of the bottom area. A further disadvantage of the
microcosm is that it cannot be miniaturized for biological applications such
as cell culturing. Also in the case of shear inducers a shear stress uniformity of
84% can be achieved under restricted conditions (very small cone tip-substrate
distances, very small Reynolds number). For more details on this issue, the
reader is referred to Javadi and Khalili (2009).
As an alternative to the devices in both categories, Khalili and Javadi
(2009) have suggested a new device (see the bottom image in Figure 10.2)
with which a shear stress uniformity over 94% or larger sections of the bot-
tom area may be generated. As shown in the figure, the system composes of a
central rotating disk, surrounded by a number of rings that rotate with lower
angular velocities. For the sake of comparison, the shear stress uniformity
achieved by all three devices are shown in Figure 10.3. Note that the calcula-
tions made for the multiring device contain a central disk and three rotating
rings.
As clearly demonstrated, the multiring device performs best. The real
advantage of the multiring device is that it can be applied to any flow and
size constraints, and can be applied for all kinds of applications both in large
and small scale.
Another issue associated with chamber flows and those in cone viscosime-
ters is the problem of artificial pressure near the interface, which affects
directly the sediment-water fluxes. This issue has to be given special attention
when the substrate is a porous sediment.
For the sake of completeness, the pressure field has been calculated and
plotted in Figure 10.4. The analysis demonstrates an almost contact pressure
for the entire radius. The pressure profile generated by the microcosm has
two distinct gradients, leading to larger differential pressure. Hence, as far
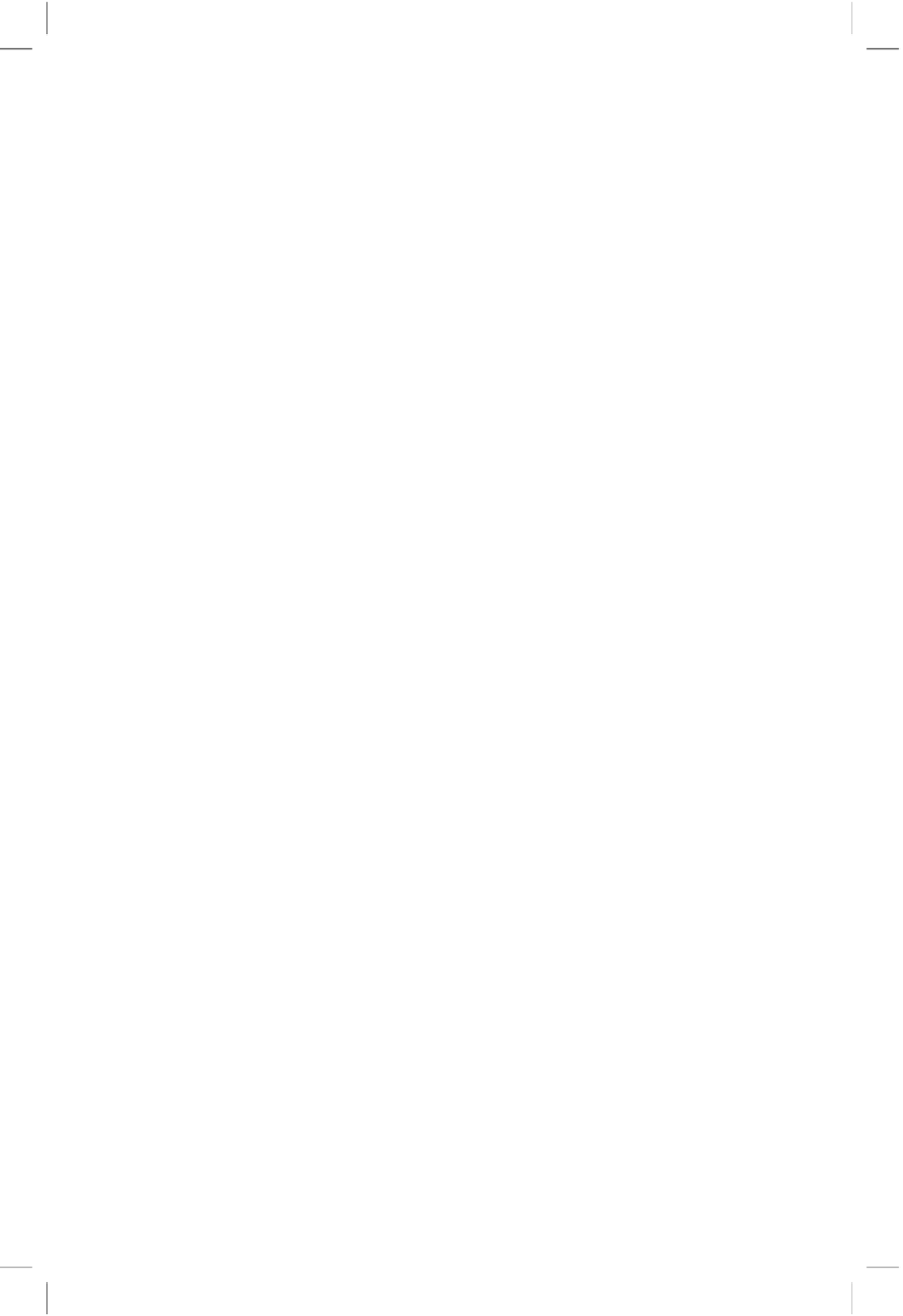
Search WWH ::

Custom Search