Biomedical Engineering Reference
In-Depth Information
3
2.5
2
1.5
1
0.5
0
0
1
2
3
4
5
6
7
8
9
Mixing time (min)
Figure 8.7
Mixing time as a function of power/volume.
sample from the top, middle, and bottom for liquid mixing. However, samples
at various locations may be required for mixing with potential product impact or
nonsteady-state condition.
Figure 8.7 shows a relationship between power/volume and mixing time to
establish mixing time and speed for a mixing process. An appropriate mixing
speed can be selected using the data on equipment capability and manufacturing
needs, including product characteristics (e.g., physical processing, shear-sensitive
solution). Higher speed and shorter time is appropriate for physical mixing,
whereas low speed and longer time would be desirable for shear-sensitive mixing.
Table 8.8 shows the RA of mixing parameters and their impacts for product pool
mixing in biologics manufacturing to develop a small-scale study. Historical data
showed that there was a decrease in filterability because of protein aggregates
formation or precipitation.
8.7.5 Example 3: Hold Times Study for Solutions and Product Pool
The chemical/biochemical stability of process solutions and intermediates should
be studied for storage time and condition. The validation approach should include
physico-chemical/biochemical stability and contamination control (e.g., biobur-
den, and endotoxin). In-process hold stability studies should be performed to
demonstrate product stability throughout specified in-process hold times and man-
ufacturing conditions (e.g., temperature, pH, etc.).
Contamination control and stability studies can be combined into one study
or performed separately. Stability of the solutions is typically performed
using scaled-down models, and assays include the measurement of chemical
attributes, such as pH, conductivity, or component concentration, over time.
The scaled-down container must be made of identical material as used in the



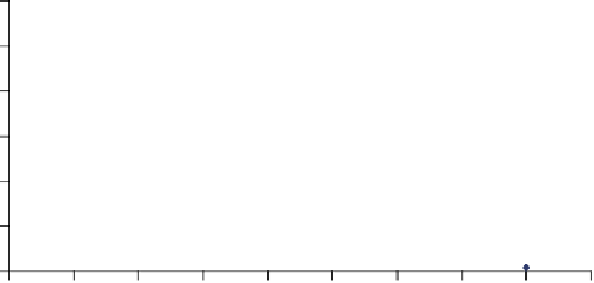






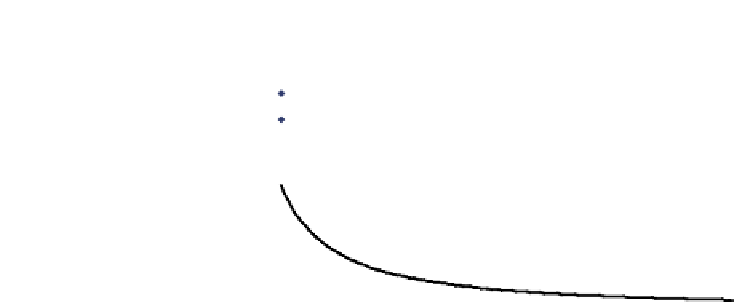







Search WWH ::

Custom Search