Biomedical Engineering Reference
In-Depth Information
the beam only traverses those areas to be exposed. In practice vector scan-
ning has proven to be somewhat faster at scanning a substrate; however, it
does require the use of a shaped beam which limits its power compared to
raster scanned beams [53].
There are several different types of direct write exposure equipment avail-
able, including excimer laser, ion beam, electron beam, and Argon laser sys-
tem. At this time there is not a preferred system, as all of the systems are
capable of producing ultrafine lines and good aspect ratio (height to width
ratios), but all are quite slow. Most photoresists currently available are sensi-
tive to radiation in the range of either 365 or 248 nm. This is because most of
the optical lithography exposure equipment available exhibits its strongest
output peaks at one of these values. Currently available resists require rela-
tively high levels of exposure so that improved resists are required that bet-
ter respond to the outputs of the direct write systems.
Laser systems using argon laser sensitive resists are in development for cer-
tain applications. The new resist films are expected to require only ∼1-5 mJ of
energy for exposure, which is about 1/10-1/100 of the current requirement.
Another area of research involves the development of a new class of resists
based on laser volatilized polymers. These are materials which can be vapor-
ized to CO, CO
2
, and H
2
O via exposure to a laser source. The resist coating
would be processed as described up to the exposure step, but the laser would
selectively destroy the resist as the pattern required. The chief advantage to
such a system is that it would eliminate the need for a developing step.
After exposure, development, and a final bake (to increase crosslink den-
sity) the imaged LiNbO
3
substrate is ready for further processing. The next
step is the coating of the piece with titanium. This may be accomplished via
resistance heated evaporators, sputtering, or electron beam process (see Figure
5.21) [54]. This step produces a uniform metal layer deposited over the entire
Substrate
holder
Substrate
holder
Substrate
Substrate
Shutter
Shutter
Electron beam
trajectory
Electron gun
Evaporation
source material
Heater
Magnetic focus
electron beam
(a)
Vacuum pumping
(b)
Vacuum pumping
FIGURE 5.21
(a) Resistance evaporation and (b) electron beam evaporation.














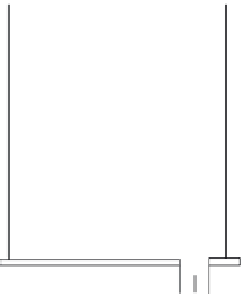









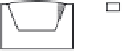



















Search WWH ::

Custom Search