Biomedical Engineering Reference
In-Depth Information
(a)
(b)
Figure 9.5
Examples of double layer Ti-HA coatings obtained with plasma spray technologies: (a) low-roughness
APS Ti coating with APS-HA coating; (b) high-porosity VPS Ti coating with VPS HA coating.
9.4 Coating Analysis Methods
According to the guidance, the coating should
exceed 22 MPa in tensile strength, 20 MPa in shear
strength, and should lose less than a total of 65 mg
(by weight) when abraded for 100 cycles.
With regard to the chemical composition of the
coating, there are no declared limits, although ASTM
F1580 indicates the chemical requirements for tita-
nium powders used for coatings of surgical implants
[59]
. As seen in Section
9.3
, the coating composi-
tions differ from those of the starting powders
because of chemical reactions with the surrounding
atmosphere. Flakes of the coating detached from the
substrate can be analyzed by means of chemical
methods such as inductively coupled plasma (ICP) to
assess the iron content and inert gas fusion (IGF) to
measure carbon, sulfur, oxygen, and nitrogen content
[60
e
62]
.
With regard to the HA coating, the ISO Standard
13779-2
[63]
specifies requirements for hydroxyap-
atite coatings applied to surgical implants, and serves
as a guideline for the characterization as well.
Various chemical and mechanical properties shall be
analyzed, such as:
For the testing of metallic plasma-sprayed coat-
ings, a guidance for industries and Food and Drug
Administration (FDA) reviewers
[53]
was released
by the Center for Devices and Radiological Health
(CDRH) in 2000, which is widely used as a reference
for coatings validation and for post-market surveil-
lance actions. CDRH requests the manufacturers of
joint prostheses to have metallic thermal spray
coatings included in the 510(k)s of new products,
with data regarding microstructure, metallurgical
aspects, and mechanical properties, such as:
l
Composition, trace elements analysis, and mate-
rial microstructure of the modified surface;
l
Photomicrographs of the microstructure of the
finished material, such as topographical scan-
ning electron microscopic (SEM) imaging and
cross-sectional images;
l
Surface thickness, void size at the surface,
minimum void size of the interconnecting
porosity, and mean volume percent of voids as
per ASTM F1854
[54]
;
l
Static tensile strength of the surface/substrate
interface, tested by either method described in
ASTM F1147
[55]
;
l
Static shear strength of the surface/substrate
interface, tested by either method described in
ASTM F1044
[56]
;
l
Shear fatigue strength of surface coating, tested
out to at least 10
7
cycles as per ASTM F1160
[57]
; and
l
Abrasion resistance of the coating, tested as
described in ASTM F1978
[58]
.
l
The content of calcium and phosphorus, that is,
the calcium-to-phosphorus atomic ratio, Ca:P;
l
The level of metals, such as arsenic, cadmium,
mercury, and lead, having adverse biological
reactions;
l
The mass fraction of HA,
a
-TCP,
b
-TCP, TTCP,
and CaO;
l
The crystallinity value of the hydroxyapatite
phase;
l
The adhesion to the substrate.
The acceptance limits are listed in
Table 9.1
.
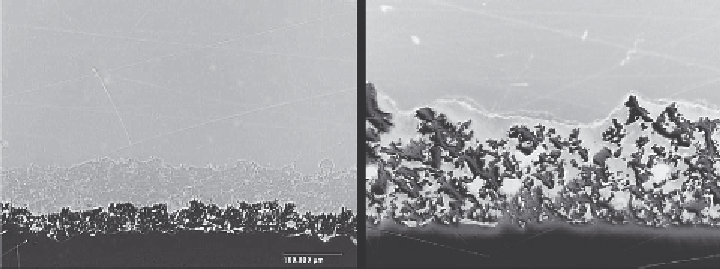