Biomedical Engineering Reference
In-Depth Information
obtained by using the so-called bimorph structure. It consists of two layers of conducting polymer
that work as electrodes and sandwich a solid polymer electrolyte. Following the application of a
voltage difference between the polymer layers, one of them is oxidized and the other is reduced.
Accordingly, they show an opposite variation of length. This causes a bending of the structure
toward the shortening side [46,75]. The length variation of the electrodes and, therefore, the result-
ing bending can be reversed when the applied potential difference varies from a positive half-period
to a negative one and vice versa.
As a different actuating confi guration, fi ber actuators made of conducting polymers have been
proposed as well. They can consist of extruded fi bers, covered by a thin layer of solid polymer
electrolyte and a counterelectrode of conducting polymer [64]. Conducting polymer fi bers have
now become commercially available. For instance, Santa Fe Science and Technology Inc. produces
polyaniline (PANi) fi bers under the trademark of Panion. They have been used to fabricate linear
actuators: a bundle of Panion fi bers (operating as an actuating electrode) has been inserted into a
Panion hollow fi ber (counterelectrode) with a separator-electrolyte medium. This kind of actuator,
tested with a [BMIM][BF4] ionic liquid electrolyte, has reported strains of about 0.3%, stresses of
about 1.8 MPa, and redox cycle lifetimes in excess of 10
4
cycles [59].
State-of-the-art devices made of conducting polymers typically need driving voltages of the
order of 1 V and are able to generate strains of the order of 1-10% for linear actuators and rotations
up to
90° for benders, with large active stresses (up to tens of MPa). Nevertheless, such interest-
ing performances usually correspond to several drawbacks, such as high response times and short
lifetimes, whose relevance has to be evaluated in relation to the specifi c application of interest.
Approaches to increase the achievable strains are currently the object of several studies. As a fi rst
method, since these materials are typically poor ion conductors, it can be useful to use thin polymer
layers and to add water-fi lled pores or tunnels in order to allow fast diffusions of ions inside the
polymer. As a second point, it can be useful to store the ions instead of transporting them. This can
be done by using a solid polymer electrolyte (electrolyte storage confi guration) or switching the
ions between two different polymer layers through a solid polymer electrolyte (electrode storage
confi guration).
In order to fabricate conducting polymer structures having the main dimensions of the order
of centimeters, different techniques have been proposed so far. They consist of classical proce-
dures borrowed from many industrial sectors, where they are employed for different uses. Elec-
trochemical deposition, casting, deep- and spin-coating are the most notable examples. They are
briefl y mentioned here. Electrochemical deposition or electropolymerization is performed by using
an electrochemical cell whose liquid electrolyte contains the monomer under polymerization. The
procedure consists of a growth of polymer layers typically via monomer oxidation. In particular, the
polymer is deposited on the electrode where oxidation takes place (anode) [76,77]. This method can
be used for direct fabrication of electrode/polymer bilayers. Alternatively, the active polymeric layer
can successively be peeled off from the deposition electrode, so that it can be coupled to another
type of passive substrate. Casting, deep- and spin-coating, and extrusion can be used for fi lm and
fi ber fabrication if the material is available in solution phase. Following the material processing
and shaping, the polymer solution is dried in an oven or by exposure to an infrared lamp. These
techniques have been largely used for polyaniline [78,79] and certain forms of polypyrrole [80-83].
Bender actuators fabricated with such techniques can present, when fatigued, a separation of the fi lm
from the support (delamination) due to shear stresses generated at the layer interface by the bending
movement during operation. Interface roughening, enriching the mechanical interlock between the
two layers, has been demonstrated as being useful in order to reduce such a problem [84].
Different techniques have been used to microfabricate small-scale conducting polymer actua-
tors, down to micron size. The most used microtechnologies consist of conventional procedures
of surface and bulk micromachining derived from photolithography. They are implemented as
sequential steps of layer depositions and etching removals [85,86]. With such methods, several
examples of bending actuators have been reported, mainly related to Au/PPy bilayers fabricated
±
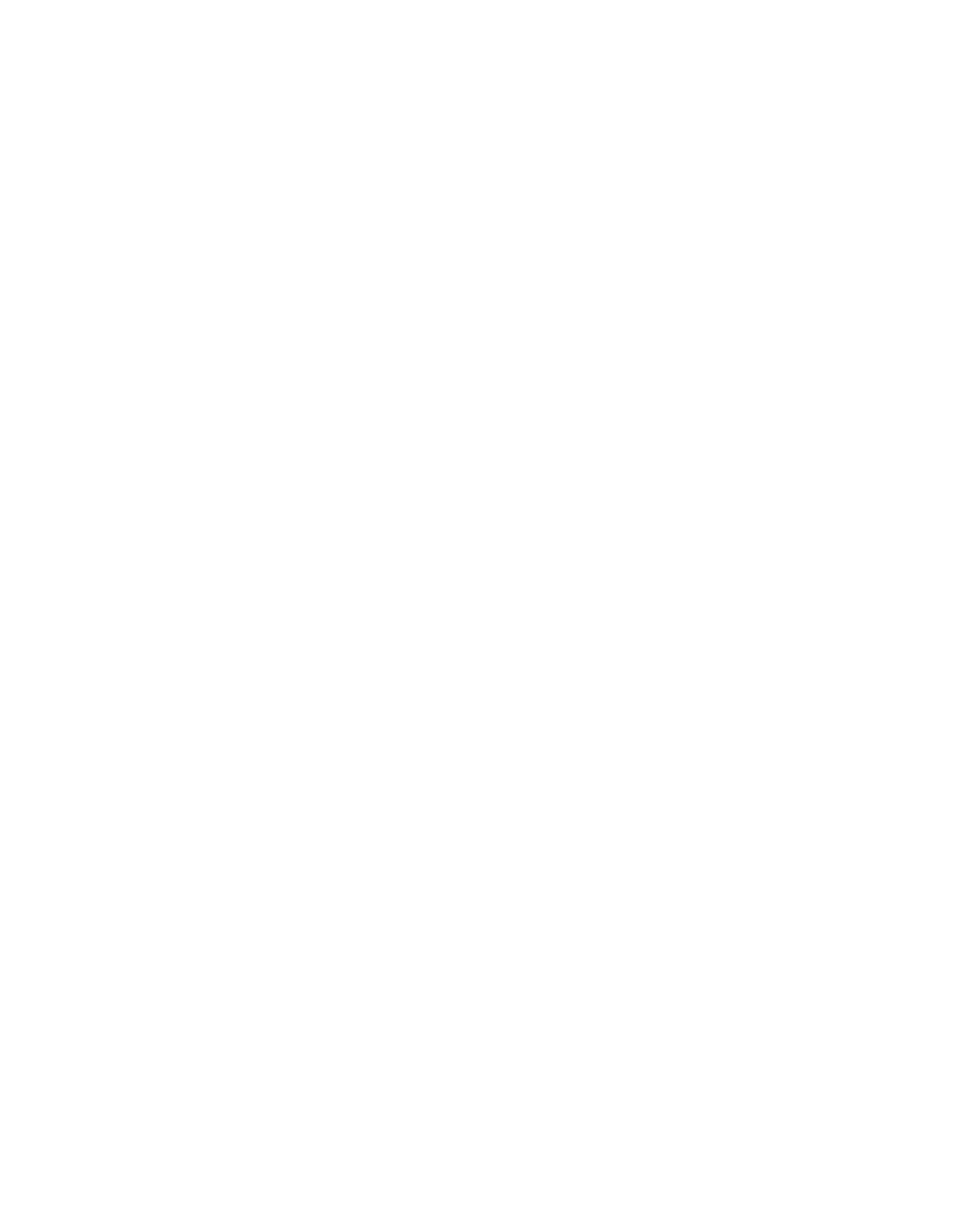