Biology Reference
In-Depth Information
built). Evaporation is performed at pressures <1
10
-6
torr. Occasionally, dur-
ing the evaporation of titanium, the pressure increases above 1
×
10
-6
torr, but
decreases after allowing the chamber to stabilize for approximately 2 min.
Allow the metals to reach evaporation rates of 1 Å/s. Allow 400-500 Å of each
metal to evaporate before opening the shutters and exposing the glass slides to
15 Å of titanium (Aldrich, Milwaukee, WI, 99.99+% purity) and 115 Å of gold
(Materials Research Corporation, 99.99 + % purity).
×
2.2. PDMS Stamp with Patterns Molded
from a Photolithographic Master
Basic lithographic techniques, concepts, and terminology are described by
Madou
(24)
. Procedures that result in thicker features are available from the
manufacturers of other types of photoresists; for the sake of brevity, we do not
describe them here. Use test grade N type, 9-13-mils thick silicon wafers
(Silicon Sense, Nashua, NH), with <100> orientation, phosphorus dopant, and
1-10 resistivity.
2.2.1. Generating Silicon Master
with Desired Pattern Using Photolithography
In a clean room (preferably Class A), clean the wafers by sonicating for
5 min successively in trichloroethylene, acetone, then methanol. Bake at 180
C
for 10 min to dry thoroughly. Spin coat (40 s @ 4000 rpm) the wafers with
approx 1-2 mL hexamethyldisilazane (Shipley) followed by Shipley 1813
positive photoresist (40 s @ 4000 rpm produces a layer of 1.3
°
µ
m); bake the
resist at 105
C for 3.5 min. Expose the wafer on a mask aligner (typically a
Karl Suss model) through a photomask with features etched in chrome depos-
ited on quartz (Advance Reproductions Corp., North Andover, MA) for 5.5 s at
10 mW/cm
2
. Develop the features by immersing in Shipley 351 for 45 s, then
rinse with distilled water and dry with a stream of nitrogen. The proper devel-
opment of the features should be checked under a microscope using a red filter
in front of the light source to avoid unwanted exposure of the photoresist. Place
the wafers in a desiccator under vacuum for 2 h with a vial (approx 1-2 mL) of
(tridecafluoro-1, 1, 2, 2,-tetrahydro-octyl)-1-trichlorosilane (United Chemical
Technologies, Bristol, PA).
2.2.2. Molding PDMS Stamp
PDMS (Sylgard 184, Dow Chemical Co.) prepolymer is made by mixing 10
parts of monomer and 1 part of initiator thoroughly in a plastic container and
degassing it under vacuum for about 1 h until air bubbles no longer rise to the
top. Pour the prepolymer in a Petri dish that contains the patterned silicon
wafer, and cure for at least 2 h at 60
°
C. Peel the PDMS from the wafer and cut
the stamps to the desired size with a razor blade.
°
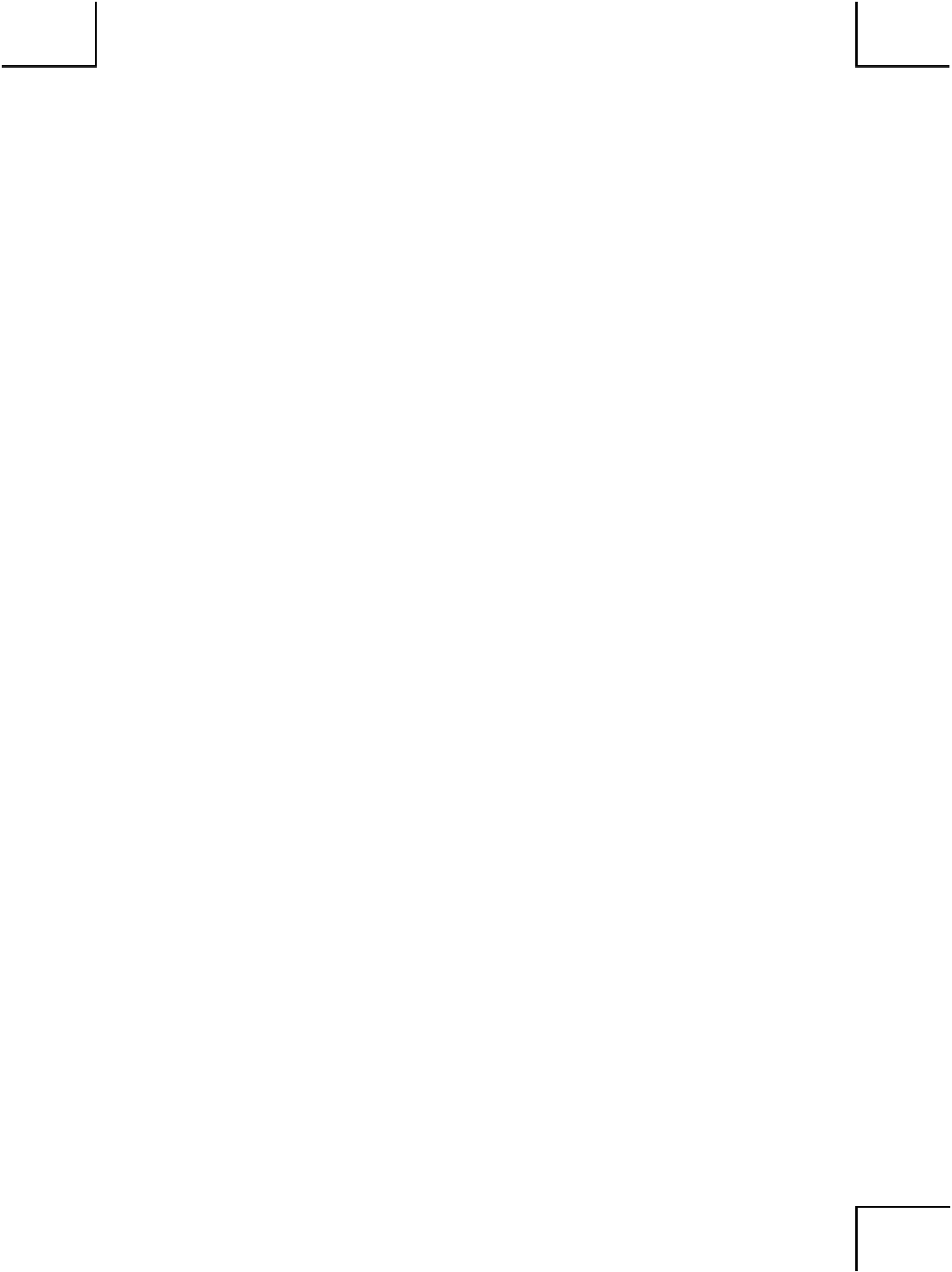
Search WWH ::

Custom Search