Environmental Engineering Reference
In-Depth Information
in airgap rather than just the stator slot gaps at the edges of full-pitched coils. The
details of these techniques are outside the intent of this topic. However, because of
the issue with cogging torque, brushless dc machines have not found widespread
acceptance as a hybrid propulsion technology, but rather are relegated to electrified
ancillary drives where very high power density, low cost and compact packaging
are the overriding considerations.
Power electronics control of BDCMs is generally accomplished through
classical 120
current conduction, or what has been referred to as block mode.
Figure 5.11 illustrates the architecture of the BDCM with trapezoidal back-emf and
rectangular current control.
Power electronics stage and heat sink
D
D
D
G
G
G
S
S
S
Surface
permanent
magnet
(SPM)
+
dc
link
cap.
D
Vehicle
energy
storage
system
D
G
D
G
G
S
S
Back-emf
voltage
sensing
S
Logic
power
supply
Gate
driver
Gate
driver
Gate
driver
Current
sense
Microcontroller and
communications
Communications network
Figure 5.11 Brushless dc motor control
Figure 5.11 shows in schematic form the major components of a BDCM drive:
(1) power electronics inverter stage and thermal management cold plate, (2) gate
driver assemblies for controlling the power switches, (3) communications, current
sensing and controller, (4) logic power supply for powering the controller, gate
drivers and sensors, (5) the dc link capacitor necessary to circulate ripple currents
from the motor and (6) the SPM motor. BDCMs for position control and applica-
tions requiring operation at zero speed will require an absolute rotor position sen-
sor. The most economical choice for rotor position sensing is the use of Hall
element sensors placed at 120
electrical intervals near the rotor magnets. The
position information from these three Hall transducers provides the microcontroller
commutation logic its timing and rotor direction information. For applications not
requiring operation at or near zero speed, it is very common for BDCMs to rely on
sensorless techniques such as back-emf sensing of the inert phase, the use of phase
voltage and bridge current signals to infer position, and various techniques based on
development of an artificial neutral.
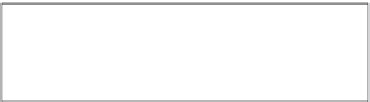




























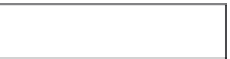
















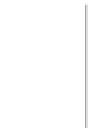




































































