Information Technology Reference
In-Depth Information
customer demand. Lowe's also uses BI to analyze customer product returns in real time to
identify potential fraudulent returns. The amount of data and transaction processing power
required is so great that Lowe's BI operation runs on some 3,000 servers.
17
Production and Supply Chain Management
ERP systems follow a systematic process for developing a production plan that draws on the
information available in the ERP system database.
The process starts with
sales forecasting
to develop an estimate of future customer demand.
This initial forecast is at a fairly high level with estimates made by product group rather than
by each individual product item. The sales forecast extends for months into the future; it
might be developed using an ERP software module or produced by other means using spe-
cialized software and techniques. Many organizations are moving to a collaborative process
with major customers to plan future inventory levels and production rather than relying on
an internally generated sales forecast.
Oberto Sausage Company is a manufacturer of meat snacks and sausage products. Its
products are sold directly to mass merchandisers and major supermarket chains in the United
States. Oberto Sausage products are also distributed globally by Frito-Lay. Eric Kapinos,
Director of Forecasting and Planning at Oberto, leads a forecasting process that is executed
by a team of individuals using sales forecasting tools. “We have a full complement of Forecast
Pro products at Oberto,” explains Kapinos, “We use Forecast Pro Unlimited as the main
foundation for our demand forecasting process—it's where the forecast is generated and
maintained. After we establish the forecast, it is fed into our ERP system where it drives
procurement, planning, scheduling, and plant execution.”
18
The
sales and operations plan
(S&OP) takes demand and current inventory levels into
account and determines the specific product items that need to be produced and when to
meet the forecast future demand. Production capacity and any seasonal variability in demand
must also be considered. The result is a high-level production plan that balances market
demand to production capacity. Air Products and Chemicals, Inc. serves technology, energy,
industrial, and healthcare customers globally with a portfolio of products, services, and so-
lutions that include atmospheric gases, process and specialty gases, performance materials,
equipment, and services. The firm operates in 30 countries with about 18,500 employees. It
uses software to support its sales and operations planning process. During S&OP meetings,
various sales scenarios and options for meeting those scenarios are evaluated based on revenue,
profit, and inventory impact, and then compared to operating plans. The advantages of this
rigorous approach are “aligned strategy and operations, improved visibility and control over
the global supply chain, fact-based planning, concentrating on exceptions and consistent
performance management.”
19
Demand management
refines the production plan by determining the amount of weekly
or daily production needed to meet the demand for individual products. The output of the
demand management process is the master production schedule, which is a production plan
for all finished goods.
Detailed scheduling
uses the production plan defined by the demand management process
to develop a detailed production schedule specifying production scheduling details, such as
which item to produce first and when production should be switched from one item to
another. A key decision is how long to make the production runs for each product. Longer
production runs reduce the number of machine setups required, thus reducing production
costs. Shorter production runs generate less finished product inventory and reduce inventory
holding costs.
Materials requirement planning
determines the amount and timing for placing raw ma-
terial orders with suppliers. The types and amounts of raw materials required to support the
planned production schedule are determined based on the existing raw material inventory
and the bill of materials or BOM, a sort of “recipe” of ingredients needed to make each
product item. The quantity of raw materials to order also depends on the lead time and lot
sizing. Lead time is the amount of time it takes from the placement of a purchase order until
the raw materials arrive at the production facility. Lot size has to do with discrete quantities
that the supplier will ship and the amount that is economical for the producer to receive
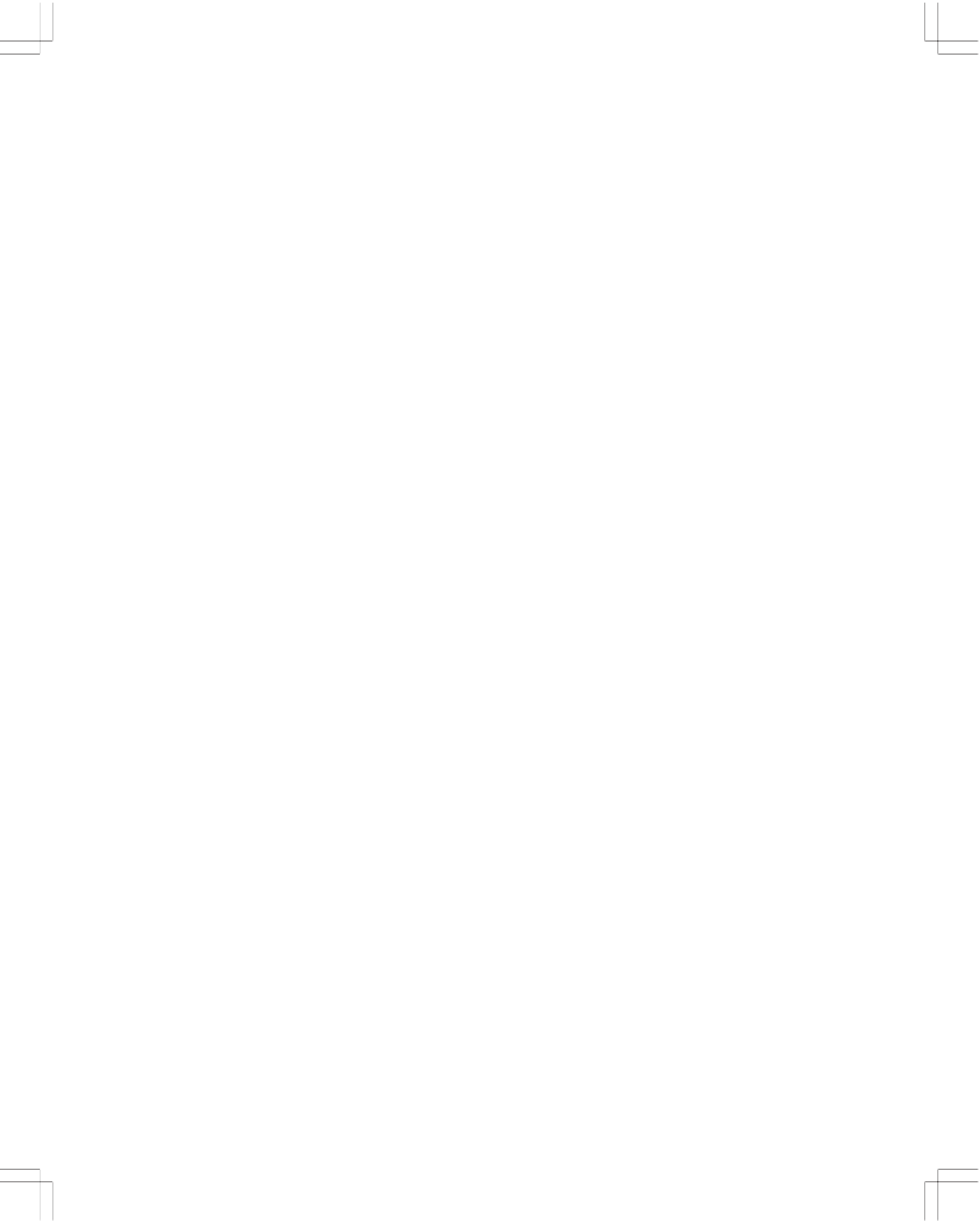