Biomedical Engineering Reference
In-Depth Information
employed in an extractor. However, high temperatures may cause deterioration and
denaturation of some oil and meal components. Hence, determination of appropriate
extraction temperature is based on the solvent properties and required specifications of the
final product.
Expanders are used to form oilseeds into porous pellets, which are commonly known as
collets. There are two types of extruders used in the oilseed processing industry, expanders
and dry extruders. Dry extruders are discussed in the mechanical expression section of this
chapter. Expanders consist of an un-segmented barrel housing a worm screw with interrupted
flights and needle valves installed at the flight interruptions to inject water or steam onto the
product stream, flaked seeds. Conversion of flaked seeds into extruded collets improves
solvent extraction efficiency. Collets are larger and stronger and have larger bulk density
than flakes. Better solvent flow and micelle (oil
solvent) drainage are achieved in the
solvent extractor when collects are used for solvent extraction. Because of the larger bulk
density of collets less space is required for the same weight oilseed in the extractor.
Production capacity in a plant is increased when collets, rather than flaked seeds, are used
for solvent extraction. High oil content seeds such as sunflower, safflower, peanut, canola
and rapeseed have too much oil to produce good flakes and collets. Hence, they are pre-
pressed to reduce meal oil content to 16-18% before solvent extraction. Soybean does not
require pre-pressing because of its relatively lower oil content (18-20%). A new screw press
design combines pre-pressing and extruded collets formation into a single processing unit.
A drainage cage and a pressing screw are included into the barrel of an expander, so there is
no need for purchasing a separate extruder and pre-press.
In the 1800 s small batch type oil extraction systems were common in Europe. The same
vessel was used for both extraction and meal desolventizing. Today, only extraction of
specialty and high value oils and recovery of oil from spent bleaching clay are carried out in
batch extractors. A rotating drum and a vertical cylindrical kettle equipped with a vapor
tight cover and a low-speed agitator are two popular batch type extractor designs.
Use of large scale continuous processes began in the early 1920s. Today, immersion and
percolation type continuous extractors are used for commercial solvent extraction of oilseeds
(Bernardini, 1976 ; Becker, 1978 ; Christensen, 1983 ; Woerfel, 1995 ). In immersion type
extractors flaked oilseeds are completely submerged in solvent. The material is gently
agitated by a screw stirrer. Micella is collected from the top of the extractor. As the extracted
material comes out of the extractor bottom it leaves the solvent bath and is conveyed to an
elevator. While moving up the elevator in a series of baskets with perforated bottoms, the
solvent is drained off and finally residual meal is delivered into a desolventizer (Becker,
1978). This type of extractor is suitable for very fine ground materials, which cause poor
drainage through the fines in other type of extractors unless the material is pelletized.
Early extractor designs based on solvent percolation were basket-type extractors in which
flaked seeds were placed in baskets with perforated bottoms. These systems looked like an
enclosed bucket elevator. The baskets were supported by endless chains in a sealed housing
and continuously raised and lowered at a slow rate (1 revolution/h). Each basket was filled
with flaked seeds by an automatic feed hopper at the top. As the basket started descending
solvent is sprayed over the baskets. The spent flakes in baskets ascended to the top of the
housing on the opposite side of the feed hopper. At the top baskets were automatically
inverted and spent seeds were discharged into a hopper, from which they were transferred to
a meal desolventizer on a conveyor belt. Basket type extractors were bulky and hard to
maintain. The newer extractor designs are horizontal and rotary type. The design principle
for horizontal extractors is similar to the basket-type extractors but the baskets rotate in a
+
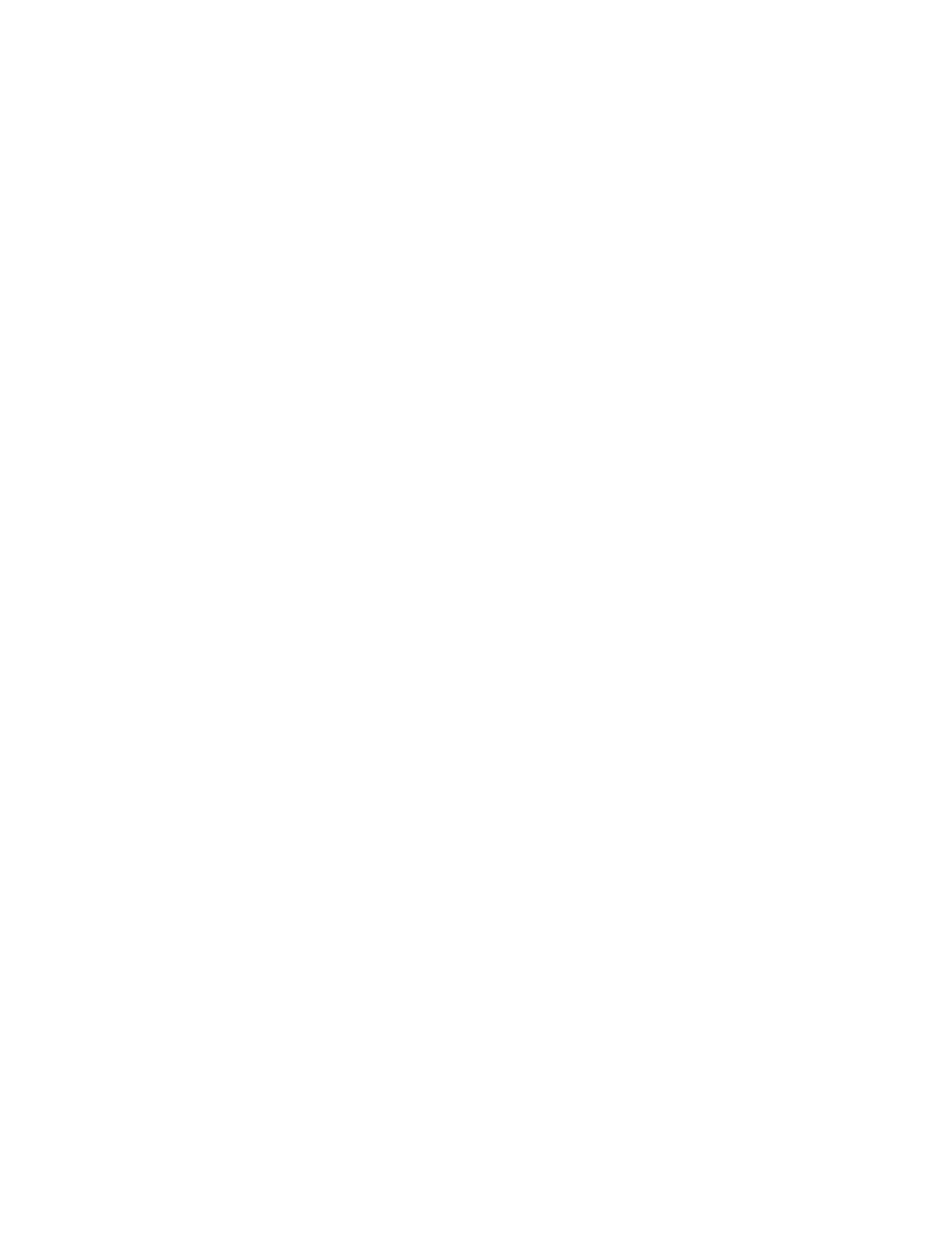



Search WWH ::

Custom Search