Civil Engineering Reference
In-Depth Information
8
7
6
5
4
3
2
1
0
0.1
0.2
0.3
F
all
/
F
y
0.4
0.5
FIGURE 6.14
AREMA minimum shear force for built-up compression member design.
6.3.3.1.6.1 LacingBarsforCompressionMembers
Thespacingoflacingbars
along the main member must be designed to preclude buckling of portions of the
main member elements between the lacing bar connections. AREMA (2008) limits
the slenderness ratio,
L
p
/r
p
, of elements between lacing bar connections to 2/3 of the
member slenderness ratio,
L/r
. This is appropriate in order to consider not only the
local buckling effects over the length,
L
p
, but the interaction between global and local
buckling (or compound buckling) (Duan et al., 2002). AREMA (2008) recommends
that the lacing bar spacing be such that
L
p
r
p
≤
40
≤
2
L
3
r
,
(6.61)
where
L
p
is the length of main member element between lacing bar connections (see
Figure 6.13a and b)
and is equal to 2
a
(for single lacing), and
a
(for double lacing),
and
r
p
is the minimum radius of gyration of the main member element.
The lacing bars on each side of the main member must be designed to resist the
shear force
V
/2 in the plane of the lacing bars. Therefore, the force in each lacing
bar is
V
2 cos
P
lb
=
.
(6.62)
φ
The critical buckling stress and minimum cross-sectional area of the bar,
A
lb
, can be
determined, using Equation 6.33 with
K
=
1.0, as
17,500
F
y
E
3
/
2
L
lb
r
lb
,
F
all
=
0.60
F
y
−
(6.63)
where
L
lb
=
√
a
2
lacing bar between connections at the main member),
L
lb
=
+
0.70
√
a
2
b
2
for double
+
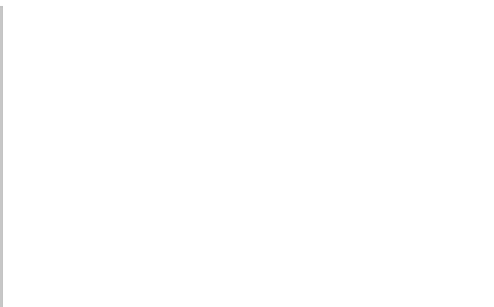
















