Biomedical Engineering Reference
In-Depth Information
GaAs capping layer
QD
2
(0.9 ML InAs)
4 nm
GaAs intermediate layer
I
QD
1
(1.2,1.4,1.5 ML InAs)
InAs QDs into GaAs
nanoholes
GaAs buffer layer
GaAs (S.I.) substrate
Fig. 1.1
Schematic diagram of the structure grown to obtain vertical QDMs. The first layer
of nanostructures (QD
1
) is formed through preferential InAs nucleation into a GaAs nanoholes
template obtained by the droplet epitaxy “nanodrilling” technique. Three samples were fabricated
by varying the amount of InAs deposited (1.2, 1.4, and 1.5 ML) to form QD
1
. By the growth
of a 4-nm-thick GaAs barrier layer and the deposition of 0.9 ML of InAs, a second layer of
nanostructures (QD
2
) is formed on top of QD
1
by a strain-driven nucleation process
of low density vertical In(Ga)As QDMs. Formed by two vertically aligned InAs
QDs, a deliberate control of size/energy emission is achieved in these nanostructures
[
31
]. Particularly, the emission energy of the first layer of QDs (hereafter referred
to as QD
1
) that forms the molecule is tuned by the preferential nucleation of
controlled amounts of InAs into etched nanoholes. After this first deposition, a thin
intermediate GaAs layer is grown in order to define a tunneling barrier that separates
a second layer of InAs QDs (hereafter referred to as QD
2
), which nucleate on top
of the first ones via a strain-driven self-assembled process [
8
-
10
]. This fabrication
procedure allows for obtaining either symmetric (the energy levels of both QDs
forming the molecule are in resonance) or asymmetric (the energy levels of both
QDs forming the molecule are out of resonance) vertically coupled structures where,
without any further technological process, the type of carrier mediating the tunnel
coupling in the QDMs can be controlled on demand.
The fabrication process for obtaining vertical InAs QDMs is illustrated in
Fig.
1.1
. Initially, a 0.5
m-thick undoped GaAs buffer layer is grown at a substrate
temperature of 580
◦
C by MBE on a semi-insulating GaAs (0 0 1) substrate. The
nanoholes template is fabricated at a substrate temperature of 500
◦
C maintaining
the Ga shutter opened during 10 s, providing a Ga flux equivalent to the growth of
GaAs at a growth rate of 1 monolayer (ML) s
−
1
. During this time, the arsenic cell is
opened periodically during 0.2 s every 0.8 s. The beam equivalent pressure (BEP)
of As
4
is fixed during the process to BEPAs
4
=
10
−
7
Torr. This process, similar
to an
arsenic-debt
atomic layer molecular beam epitaxy (ALMBE) growth [
41
],
results in Ga droplets spread all over the surface with a density of 2.5
5
×
10
8
cm
−
2
.
The sample is then annealed under As
4
flux during 6 min. Once irradiated with
As
4
, the “nanodrilling” etching process stops and the Ga droplets crystallize into
GaAs, yielding a template of nanoholes surrounded by mounds. As shown in
the atomic force microscopy (AFM) image of Fig.
1.2
, these nanoholes show an
elongated morphology along the GaAs [1
×
−
1 0] crystallographic direction as a result


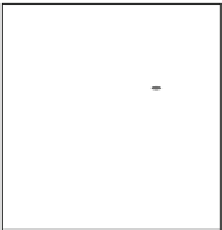









