Biomedical Engineering Reference
In-Depth Information
is developed by washing off the UV-exposed or -unexposed regions. When the substrate
is subjected to chemicals, the photoresist would protect the surface below it and thus
transfer the pattern to the substrate. A new pattern transfer method called microcontact
printing has been recently reported. This method uses a conventionally microfabricated
master to form a soft stamp by molding a polymeric substrate such as PDMS. The stamp
is “inked” with alkanethiols or alkylsilanes and placed on a gold or silicon oxide coated
surface, respectively. The printing process transfers the molecules from the stamp to the
substrate, where patterned self-assembled monolayers can then be used as resists for
etching or as passivation layers to prevent deposition. This method of pattern transfer is
advantageous when handling non-cleanroom-compatible materials or chemicals, or non-
planar substrates, although multilevel pattern registration is still unresolved.
Etching
As mentioned above, lithography is always followed by an etching step in order to
obtain a patterned fi lm or selective material removal from the substrate. Etching can be
divided into wet or dry etching. In general, wet etchants are by and large isotropic in
reactivity which etches in all directions equally, but shows superior material selectivity
as compared to dry etching techniques. An extremely important exception to this rule is
the anisotropic wet etching of monocrystalline substrates. The typical anisotropic sili-
con etchants are potassium hydroxide (KOH), ethylene diamine pyrochatechol (EDP),
and tetramethyl ammonium hydroxide (TMAH). These etchants attack silicon along
preferred crystallographic directions. Dry etching, especially reactive ion etching (RIE)
is a combination of physical and chemical processes, where the active species react
with the material only when the surfaces are activated by the collision of incident ions
from the plasma. In some cases, sidewall passivation methods (such as DRIE) are used
to further increase etch anisotropy. In this method, an already etched pit is coated with a
passivation layer of polymer and followed by ion bombardment. Since ions are directly
attacking the bottom of the pit, etching the bottom polymer and a thin layer of underly-
ing substrate, the sidewall is kept intact and thus high aspect ratios would be achieved.
Substrate bonding
Substrate bonding refers to bonding two substrates such as silicon-silicon, silicon-
glass, and glass-glass to fabricate complex 3D structures. A common example is the
bonding of a glass capping wafer to a structured silicon wafer to form an optically
accessible seal system. The two most popular bonding techniques are fusion bonding
and anodic bonding. Fusion bonding is aimed primarily at bonding two silicon wafers
via chemical reactions between the bonding surfaces, i.e. by contacting two ultraclean
hydrophilic surfaces and annealing them at high temperature (800-1000ºC). Hydrogen
bonds formed will join the substrate together. Other studies reveals that fusion bonding
can also work with silicon oxide and nitride surfaces. Anodic bonding is a widespread
method for microsensor packaging and device fabrication. This bond occurs between
borosilicate glass (Pyrex 7740) and a silicon wafer through a cooperation of a high
electric fi eld, high pressure, and high temperature (400ºC). During this period, Na
in
the borosilicate glass migrates towards the cathode under the function of electric fi eld,
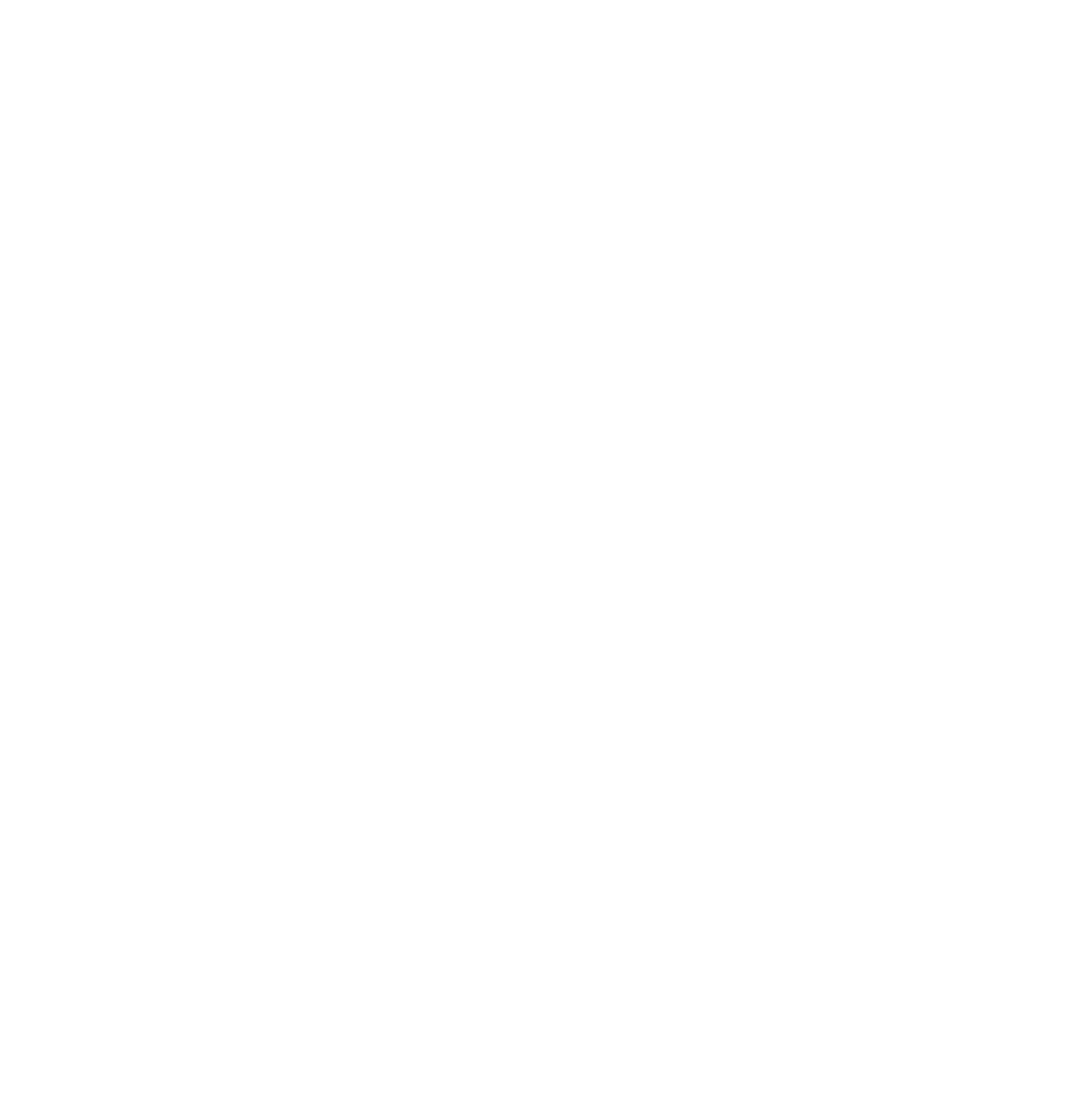




Search WWH ::

Custom Search