Biomedical Engineering Reference
In-Depth Information
the not so-desired intermetallic phases; remelting or extrusion seem
to be necessary for the microstructure improvement.
Figure 8.26
Composition with 50 at.% of Ni, SHS longitudinal views of
synthesized parts at different preheating temperatures and
compaction pressures (a) 200
o
C, 70 MPa, (b) 200
o
C, 140
MPa, (c) 200
o
C, 210 MPa, (d) 300
o
C, 70 MPa, (e) 300
o
C, 140
MPa, (f) 300
o
C, 210 MPa [44].
Cold pressing and sintering for elemental powders do not
guarantee high-quality product. The shape memory effect remains,
but obtained mechanical properties are low, and compact densities
exceed the level of 80% of theoretical volume. Furthermore, sintering
can reduce density. This is referred to as the Kirkendall effect, which
creates large pores or even craters at the surface. Hot pressing in
vacuum conditions showed that it is possible to obtain higher densities
and lower level of impurities. Ductility of the obtained materials is
locate in the range of that of wrought materials; unfortunately the
oxygen level turned out to be too high for proper
M
s
temperature
control or acceptable characteristics of fatigue resistance. The shock
compaction adapts successfully for pre-alloyed powders, gives 98%
of theoretical densities, and proceeds with the subsequent sintering,
which produces 100% densities.
By emphasizing applications, the received porous structures of
Nitinol may have beneicial aspects for medical implants. Bony in-
growth abilities combine with shape memory characteristics, good
corrosion resistance, and biocompatibility of the material, which are
crucial for this particular application.

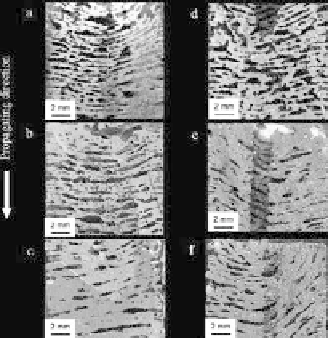














