Biomedical Engineering Reference
In-Depth Information
and synthetic non-woven textiles. Interest in the technique increased
dramatically in the mid-1990s when it was reported that the technique
could be refi ned to produce fi bers as thin as 10 nm in diameter out of a
wide variety of materials [52, 53]. Subsequent investigation has explored
a range of fi ber compositions, techniques for orienting the fi bers, and for
varying the pore size of the fi ber mats.
The basic electrospinning apparatus is relatively simple (Figure 4.2a).
A dissolved polymer in a volatile solvent is ejected from an electrically
charged needle towards a collector target. The difference in electrical
(
a
)
Syringe driver W/sample
(
b
)
High voltage
power supply
Metallic needle
Motor
Mandrel-like collector
Plate collector
(
c
)
(
d
)
Co-axial spinerets
Dual collectors
(
e
)
10
μ
m
Figure 4.2
A basic electrospinning apparatus (a) consists of an electrically
charged needle ejecting a polymer-solvent solution towards a collector plate.
This basic design can be modifi ed to produce aligned fi bers though changes in
the collector geometry (b, c), or used to fabricate composite nanofi bers though
co-axial needle designs (d). A SEM micrograph of typical PLA electrospun fi bers
shows a highly porous mat of fi bers ~1 micron in diameter (e). Adapted from
Zhang
et al.
, 2012 [117], Copyright © 2012 Elsevier Inc.
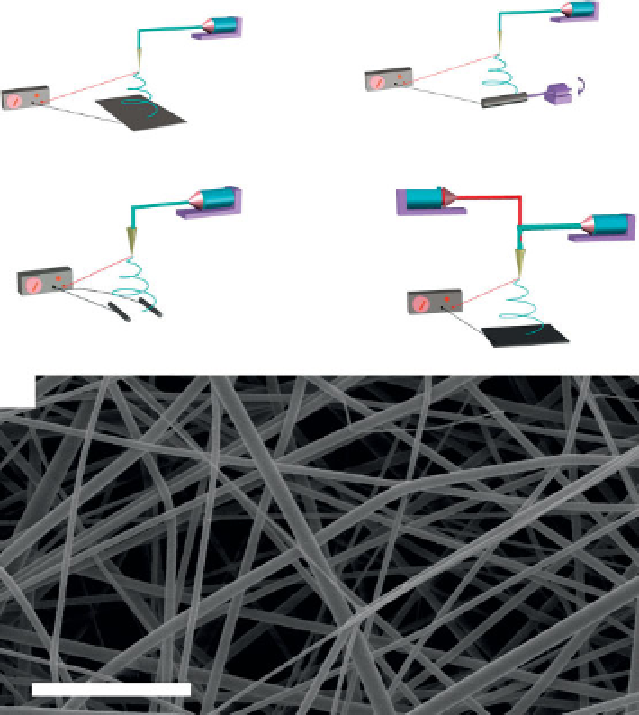
Search WWH ::

Custom Search