Biomedical Engineering Reference
In-Depth Information
hand-guided fashion. Contact pressure control places the coil gently on the head
and guarantees that the coil has contact with the head. Furthermore, it maintains an
optimal contact pressure for patient's comfort throughout the application. Addi-
tionally, the FT-readings are monitored to stop the robot in an error case.
5.2.1 Setup
Extending the robotized TMS system, we mount a Mini45 force-torque sensor
(ATI Industrial Automation, Inc., Apex, NC, USA) having six DOF between end
effector of the Adept robot and tool. Figure
5.2
shows the coil clamp mounted to
the force-torque sensor's tool side.
The sensor's optimal sensing range is up to 145 N for forces and up to 5 Nm for
torques [
1
]. It has a bandwidth of 16 bit and a resolution of 62.5 mN and
1.3 mNm, respectively. The sensor's size is 45 mm in diameter with a height of
16 mm. Hence, the sensor fits well onto the Adept robot's end effector, as shown in
Fig.
5.2
.
5.2.2 Hand-Assisted Positioning
For the current implementation of a robotized TMS system, the target accessibility
is strongly limited due to the restriction of allowed robot trajectories. Therefore,
manual pre-positioning is required, frequently. To overcome the complex pre-
positioning with the robot controller, we implement a hand-assisted positioning
method which is based on the user applied forces and torques to the coil. Sub-
sequently, these values are directly transferred into robot movements such that the
robot moves the coil in a hand-guided mode.
Fig. 5.2 A Force-Torque
sensor (A) is installed
between robot effector
(B) and TMS coil clamp (D).
The coil (C) (a MCF-B65
static cooled butterfly coil) is
fixed in the clamp (D),
attached to the sensor (A).
The TMS coil is connected to
the stimulator via a flexible
supply cable (E)
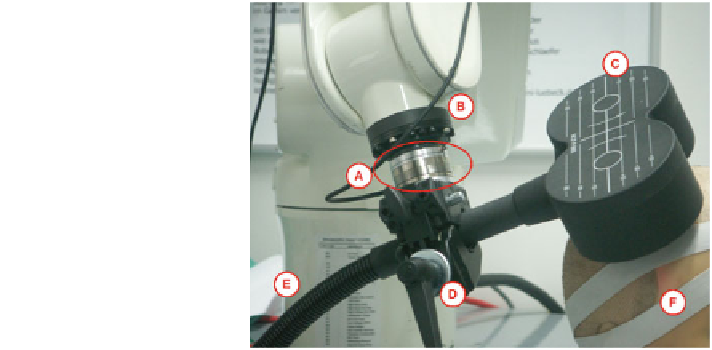
Search WWH ::

Custom Search