Biomedical Engineering Reference
In-Depth Information
(die drawing) have been applied to increase the orien-
tation of polymer chains and thus produce high-strength,
high-modulus materials (
Ferguson
et al.
, 1996
). More
recently, an extrusion process has been successfully
combined with the SC/PL technique to manufacture
porous tubular scaffolds for guided tissue such as pe-
ripheral nerve regeneration (
Widmer
et al.
, 1998
). First
the dry polymer/salt composite wafers obtained from SC
are cut into pieces and placed in a customized piston
extrusion tool (
Fig. 7.1.4-3
). The tool is then mounted
into
processing temperature. The temperature is allowed to
equilibrate and the polymer/salt composite is then ex-
truded by applying pressure. The extruded tubes are cut
to appropriate lengths. Finally, the salt particles are
leached out to yield highly porous conduits.
The pressure for extrusion at a constant rate is de-
pendent on the extrusion temperature. High tempera-
ture may result in thermal degradation of the polymer.
The porosity and pore size of the extruded conduits are
determined by salt weight fraction, salt particle size, and
processing temperatures. The fabricated conduits have
an open-pore structure and are suitable for incorporation
of cells or microparticles loaded with tissue inductive
factors.
a
hydraulic
press
and
heated
to
the
desired
1
Freeze-drying
2
Low-density polymer foams have been produced using
a freeze-drying technique (Hsu
et al.,
1997). Polymer is
first dissolved in a solvent such as glacial acetic acid or
benzene to form a solution of desired concentration. The
solution is then frozen and the solvent is removed by
lyophilization under high vacuum. Several polymers in-
cluding PLGA and PLGA/PPF have been prepared into
porous foams with this method. The foams have either
leaflet or capillary structures depending on the polymer
and solvent used in fabrication. These foams are generally
not suitable as scaffolds for cell transplantation. Sub-
sequent compression of the foams by grinding and ex-
trusion can generate matrices with varied densities. Foam
density has been shown to determine the kinetics of drug
release from these matrices.
An emulsion freeze-drying technique has also been
developed to fabricate porous scaffolds (Whang
et al.,
1995). In this technique, water is added to a PLGA/
methylene chloride solution and the immiscible phases
are homogenized. The created emulsion (water-in-oil) is
then poured into a copper mold maintained in liquid ni-
trogen (
196
C). After quenching, the samples are
freeze-dried to remove methylene chloride and water.
Using this technique, PLGA foams with porosity in the
rangeof 91-95% and median pore diameters of 13-35
m
m
with larger pores greater than 200
m
m have been made by
varying processing parameters such as water volume
fraction, polymer weight fraction, and polymer molecular
weight. Compared to the SC/PL technique, this method
produces foams with smaller pore sizes but higher specific
pore surface area and can produce thick (
>
1 cm) foams.
3
4
5
6
7
Fig. 7.1.4-3 Piston extrusion tool for the manufacture of tubular
polymer/salt composite structures: 1, extruded polymer/salt con-
struct; 2, nozzle defining the outer diameter of the tubular con-
struct; 3, tool body; 4, melted polymer/salt mixture; 5, rod defining
the inner diameter of the tubular construct; 6, heat band with
temperature control; and 7, piston moving the melted polymer/salt
mixture. The arrows indicate the attachment points for the forces
involved in the extrusion process.
Phase separation
The ability to deliver bioactive molecules from a degrad-
ing polymer scaffold is desirable for tissue regeneration.
However, the activity of the molecule is often dramatically
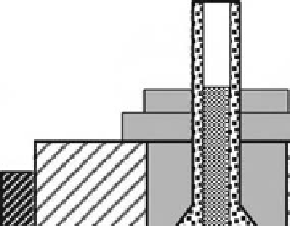
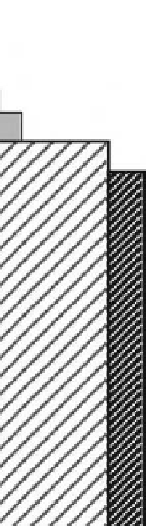

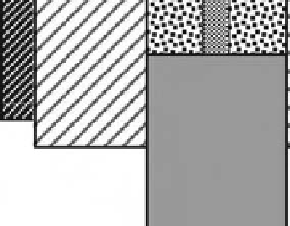










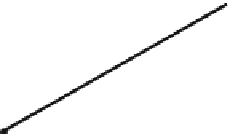
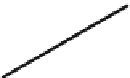

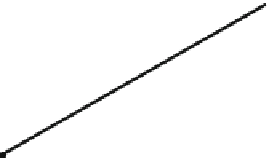





