Environmental Engineering Reference
In-Depth Information
1.2.4 Fatigue
The premature fracture of materials under fl uctuating load (stress/strain/
temperature) is known as fatigue. Fatigue is a sudden failure exhibiting no
overall ductility in the component and is known to be the cause in 90%
of the total failures of structures. During each fatigue cycle the material
absorbs part of the applied energy and, when the accumulated strain energy
reaches the value of the surface energy of the material (in that environ-
ment), a surface forms (i.e. a crack appears). The accumulation of strain
energy is facilitated by the presence of a notch or scratch and the surface
energy is the minimum for the exposed crack than the embedded one. Often,
the fracture surface is perpendicular to the direction of the applied stress
and a compressive residual stress is benefi cial in delaying the fatigue failure.
Fatigue life is represented by a plot of applied stress (
S
) against the number
of cycles to failure (
N
f
) known as the
S
-
N
curves. Figure 1.6 depicts the
S
-
N
curves for various metals
8
and we note that ferrous metals exhibit a distinct
'endurance' limit below which fatigue failures do not occur whereas non-
ferrous metals do not seem to exhibit such a limit, albeit the slope of the
S
-
N
curve decreases at very high cycles. The stress axis can also be either the
stress amplitude (
σ
max
−
σ
min
)/2, the stress range (
σ
max
−
σ
min
) or mean stress
(
min
)/2 and it is generally seen that the fatigue life depends weakly on
the
R
ratio (
R
=
σ
max
+
σ
min
represent the maximum and
minimum stresses, respectively. Depending on the number of cycles to fail-
ure the fatigue curve is classifi ed as low cycle fatigue (LCF) and high cycle
σ
min
/
σ
max
), where
σ
max
and
σ
500
1045 Steel
2014-T6 aluminum alloy
Red Brass
400
300
200
100
0
1.E+03
1.E+05
1.E+07
Cycles to failure, N
1.E+09
1. 6
S-N curves for ferrous and nonferrous metals.
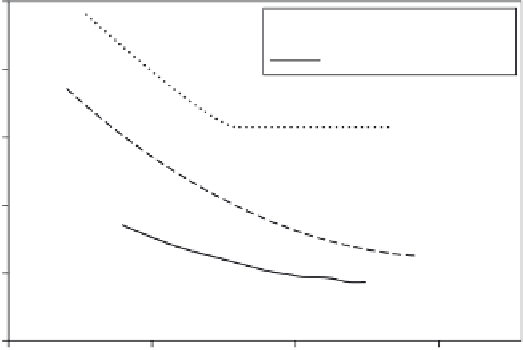

Search WWH ::

Custom Search