Environmental Engineering Reference
In-Depth Information
44%
Reverse osmosis
6%
Multistage flash
16%
Electrodialysis
9%
Multieffect distillation
41%
figurE 23.2
Major desalination technologies and their relative contributions to worldwide installed capacity for seawater and brackish
water desalination. MSF accounts for 44%, Ro 41%, and 15% is shared by other thermal methods like MED (9%) and ED (6%) [7, 9].
the world to produce drinking water from brackish groundwater and seawater, and also to improve the quality of existing
supplies of freshwater for drinking and industrial purposes, apart from the treatment of industrial and municipal wastewater
prior to discharge or reuse. In the early 1950s, about 225 land-based desalination plants were installed worldwide with a
combined capacity of about 27 million gallons per day (mgd) of waste water treatment. Today there are about 3500 plants
worldwide with a production capacity of about 3000 mgd. As the demand for freshwater increases and the quality of existing
supplies deteriorates, the use of desalination technologies will increase [8] significantly.
Membrane-based Ro or thermal-based multistage flash (MSF) and multieffect distillation (MED) contribute to over 90% of
the global desalination capacity. Ro plants, with typical capacities of approximately 20,000 m
3
/day, account for approximately
41% of the total desalination capacity, while MSF plants, with typical capacities of approximately 76,000 m
3
/day, account for
approximately 44%. other technologies, such as electrodialysis, account for only a small fraction (~5.6%) of the desalination
capacity and are more suited for applications in brackish and groundwater treatment. The system-level schematics of the differ-
ent types of desalination plants and their relative installed capacities are shown in Figure 23.2.
23.3
aquaPorins
Aquaporin is a well-known membrane-bound water channel found in all known living systems [10]. It allows water to pass
from it as a single molecule; actually, aquaporins are so selective that they will exclude the passage of any sort of contam-
ination including bacteria, virus, protein, DNA, salts, reagents, and even dissolved gases [11]. The technology is based on
a discovery that was awarded the Nobel Prize in chemistry in 2003. Profesor Peter Agre is a molecular biologist from the
Johns Hopkins University in Baltimore, the United States, who discovered during his studies that there is a special protein
that is responsible for the rapid permeation of water in cells. Agre and his team named these proteins “aquaporins,” as they
function as water pores on the nanoscale [12]. In plants, they work like the plumbing system of cells and ensure a highly
efficient but selective transport of water; only H
2
o molecules can pass through these channels [13]. For plants, these filters
are a lifesaver, as they ensure that the cell does not lose any minerals [14]. This specificity of aquaporin can be harnessed
to prepare selective filter membranes for water purification. Some bacterial aquaporins, like aquaporin Z (ApqZ), could
be candidates to design and develop nanomembranes because of their ruggedness and stability at high voltage, heat, deter-
gent, and pH. Under natural systems, aquaporins move water from areas of low dissolved solids to areas of high dissolved
solids; however, when a pressure is applied, the process can be reversed, similar to Ro. Some commercial settings of
ApqZ are now available [15]: they are inserted into 5 nm thick and 200 nm diameter polymer vesicles (Fig. 23.3). The
highly concentrated proteins are deposited on inexpensive nitrocellulose filters and cross-linked to one another with
ultraviolet (UV) light.
A European research project named MEMBAq, led by Professor Claus Helix Nielsen and his team at the Technical University
of Denmark, has undertaken further challenges to develop an aquaporin-based commercial technology for water purification
[17]. According to them, the stability of the protein and the construction of a durable filter membrane are still very difficult to
achieve. A thin film of perforated Teflon is used to further support the protein-bound membrane. later, another layer made of
porus hydrogel is constructed, which further stabilizes the membrane.
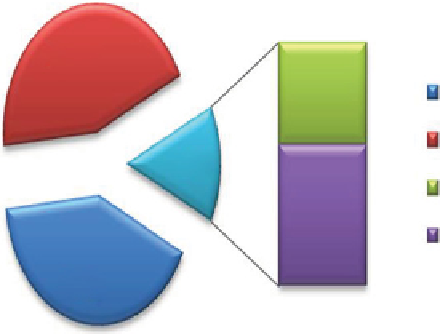