Environmental Engineering Reference
In-Depth Information
Bild 323
Herstellverfahren von Linoleum (Darstellung nach [37]).
Im Produktionsprozess (siehe Bild 323) wird heute zunächst das Leinöl zu Leinölfirnis oxidiert.
Dazu wird das Leinöl unter Zugabe der Trockenmittel in Reaktoren gerührt, mit Luftsauerstoff
beaufschlagt und auf ca. 80°C erwärmt. Nach dem Erreichen einer bestimmten Viskosität - und
damit einem bestimmten Vernetzungsgrad - der Leinölmatrix werden die aufgeschmolzenen
zusätzlichen Harze (Kopal-, Dammarharz, etc.) zugegeben und danach Aufheiz- und Abkühl-
zyklen durchlaufen, bis die gewünschte Endviskosität des Linoleumzements erreicht ist. Dieser
wird vor der weiteren Verarbeitung zwischengelagert und danach mit Korkmehl, Holzmehl,
Farbstoffen und Füllstoffen versehen. Von der Durchmischung des Linoleumzements mit den
restlichen Rezepturbestandteilen hängt die Qualität des Linoleums ab. Eine typische Rezeptur
besteht aus 40 % Gewichtsprozent Linoleumzement, 40 % Gewichtsprozent Kork- und Holz-
mehl und 20 % Kreide und Pigmente.
Die Linoleumdeckmasse wird nach der Durchmischung auf Kalanderwalzen auf den Juteträger
aufgetragen und geglättet. Durch entsprechende Steuerung der Kalanderwalzen können be-
stimmte Muster auf der Oberfläche des Linoleums erzeugt werden. Nach dem Kalander wird
die sogenannte Linoleumbahn in eine Reifekammer gefahren, die bis zu 20.000 laufende Meter
aufnehmen kann. Dort vernetzt das Leinöl unter Temperatureinfluss weiter bis die für die An-
wendung notwendige Festigkeit erreicht ist. Je nach Dicke des Linoleums dauert dies zwei bis
vier Wochen.
Danach wird das Linoleum entweder mit einem Schutzüberzug auf Acrylbasis versehen oder
unbehandelt ausgeliefert. Unbehandeltes Linoleum wird beispielsweise in Sporthallen verlegt
und dort mit einem rutschhemmenden Mittel bearbeitet oder bauseitig mit natürlichen Produk-
ten wie Wachsen behandelt.
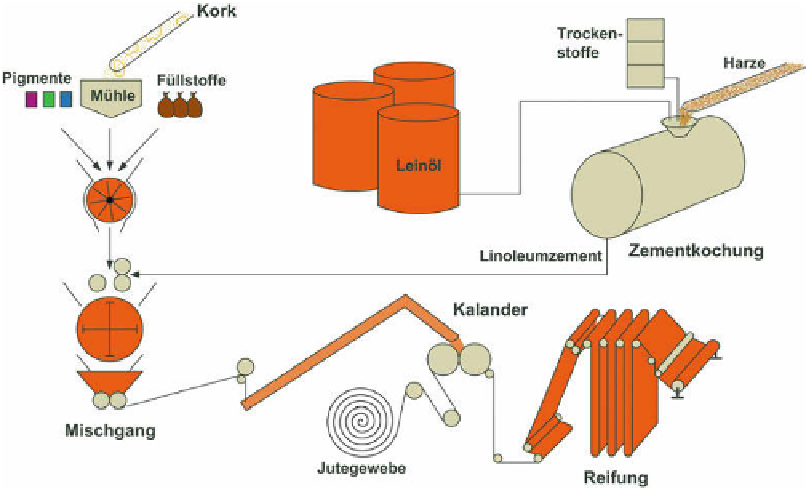

Search WWH ::

Custom Search