Environmental Engineering Reference
In-Depth Information
Clean flue
gas to stack
Reheater
Mist eliminator
Slurry spray
nozzles
Scrubber tower
Boiler
Flue gas
with SO
2
ESP
Ground
limestone
Pump
Scrubber
slurry
Thickener
Recycle
water
Overflow
tank
Make-up
water
Dewatering
and disposal
Pump
Pump
Figure 5.11
Wet limestone scrubber, schematic.
from where it has to be removed mechanically; the slurry of lime and limestone is highly corrosive;
the dewatering system is prone to breakdowns; the dewatered sludge is difficult to transport to the
disposal site. Frequent outages may still be experienced, and because power plants cannot afford
to install dual systems, during scrubber outages the SO
2
containing flue gas is simply bypassed
directly into the smoke stack.
The sorption of SO
2
by limestone is far more complete in the aqueous slurry of the wet scrubber
than in fluidized bed combustion or sorbent injection. A well-designed wet scrubber can remove as
much as 90-99% of the sulfur in the flue gas. Its power requirements (pumps, filters, reheater, etc.)
may syphon off 2-3% of the power plant's electrical output, thereby reducing the overall thermal
efficiency by the same amount. Its amortized capital and operating cost may add 10-15% to the
electricity generating cost.
Dry Scrubber.
The chemical reaction mechanism in the dry scrubber is similar to that in the wet
scrubber; that is, CaCO
3
, CaO, or both are used to absorb SO
2
from the flue gas, forming a mixture
of calcium sulfite and sulfate. The difference is that in the dry scrubber the sorbent is introduced as
a very fine spray of an aqueous slurry. The hot flue gas is blown countercurrent against the slurry
spray. The proportions of slurry and flue gas are carefully metered, so that the slurry completely
evaporates within the scrubber. In such a fashion, a dry powder of calcium sulfite, sulfate, and
unreacted sorbent is created. Here, the particle removal system, usually a fabric filter, is installed
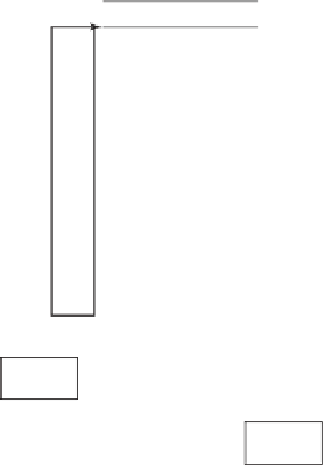

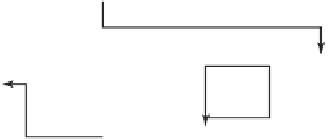
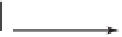











