Environmental Engineering Reference
In-Depth Information
(a)
(b)
Preheated SW
ermocompressor
Motive steam
Compressed steam
Preheater
Makeup
Sucked steam
Drain
Compressed
steam
Freshwater
Vacuum
1
Steam
2
N
Seawater
Brine
discharge
(heat recovery)
Vapor
Saline
feed
Blowdown
Distillate
FIGURE 27.5
Schematic representations of basic unit processes involved in VC cycles for water desalination: (a) TVC system
and (b) single-stage mechanical VC system. (Based on Trieb, F., ed.
Concentrating Solar Power for Water Desalination
.
ed. G.A.C. [DLR] and I.O.T. Thermodynamics. Federal Ministry for the Environment, Nature Conservation and
Nuclear Energy: Stuttgart, Germany, 2007.)
processes involved in VC cycles for water desalination. Mechanical vapor compression
or MVC units are generally single-stage plants with a production capacity up to 3000 m
3
/
day. MVC systems typically operate as single-stage units, as only the capacity and not the
eficiency is increased with additional stages [23]. In the case of thermal vapor compres-
sion or TVC plants, multiple stages are used owing to increased eficiency with designed
capacities up to 36,000 m
3
/day [22,23]. VC systems generate the heat for evaporation by
compressing feed vapor as the heat source for the heat exchanger (i.e., changes in density)
as opposed to mechanically produced heat steam as in MSF and MED [24]. In TVC units,
steam ejectors are used for VC whereas in MVC units, a mechanical compressor is used
[22]. VC is often coupled with MED systems, which increases the eficiency of the system
while raising the steam pressure requirement [22].
27.2.3.4 Reverse Osmosis
In contrast to the thermal processes discussed thus far, another class of water desalination
system arises from iltration technologies relying on the use of polymeric membranes.
Membrane systems [25] are becoming increasingly popular because of the low cost of
polymeric membranes and relatively higher energy eficiencies. The water industry exten-
sively uses membrane processes for pretreatment iltration depending on particle size (e.g.,
microiltration, nanoiltration, or ultrailtration), as depicted in Figure 27.6. Particles rang-
ing in size from a few angstroms to 10 microns can be removed by iltration processes
such as microiltration, ultrailtration, nanoiltration, electrodialysis reversal (EDR), and
RO [26,27] at varying operating pressures as described in Figure 27.6a, with the length
scales of relevant particles described in Figure 27.6b. Conceptual treatment of ions as hard
spheres allows for iltration to work with ionic salts similar to particles if small enough
pores are used in membranes. This model led to the development of RO desalination, and
the irst commercial RO plant began operation in 1965. In RO, a semi-permeable membrane
separates the feedwater from the efluent stream. RO works by pressurizing the saline
feedwater to a pressure larger than the osmotic pressure of the solution, causing the semi-
permeable membranes of the system to reject most of the solute (in this case, mostly salts)
while allowing solvent (freshwater) to pass through [22]. A schematic of the RO process is
shown in Figure 27.7. Since osmotic pressure is determined by the salinity of the feedwater,







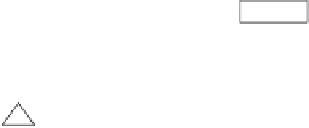

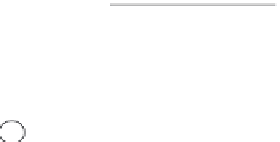




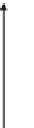
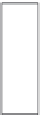


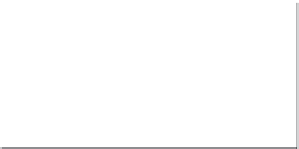








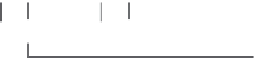













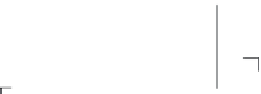


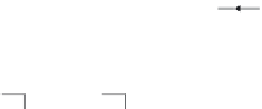
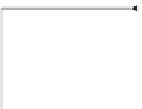










