Environmental Engineering Reference
In-Depth Information
difficult to achieve. Reliability is generally low but may be partially compensated for by
the installation of a relatively large number of gages on a given member.
Encapsulated gages
are factory waterproofed and should have a service life of about a
year or more if installed properly. Installation is simple, but as with normal bonded gages,
lead wires require protection.
Unbonded, encapsulated gages
are simple to install and have a reliability much higher than
other types. Carlson strain meters installed in concrete dams have performed successfully
for periods of over 20 years. They are also left inserted in boreholes to measure rock
stresses. Deflection ranges, however, are somewhat less than that of the other types.
Vibrating-Wire Strain Gage
Installation is simple and the gages are recoverable, remote-reading with excellent long-
term stability, strong, and waterproof. The gage, however, is a large instrument and its
measurement range is more limited than that of the resistance-gage types. Its cost is gen-
erally higher than that of most resistance gages.
Mechanical Strain Gages
Mechanical strain gages are used to measure deformations of accessible metal surfaces.
They have two pointed arms that fit into conical holes (gage points) drilled or punched
into the surface to be measured, or into studs that are set into or on the surface. The change
in distance between gage holes is measured by determining the distance between arms
when inserted into the gage points. Measurement is done with a dial gage. Wittier gages
are a popular type. Gage lengths of 2 to 80 in. are available. 10-in.-long gage is used for
most engineering studies; sensitivity is of the order of 10 microstrains, and gages are read
usually to the nearest 0.0001 in.
Mechanical gages are relatively simple and reliable. Temperature corrections are easily
made and gage calibration is easily checked. However, they are suited only for measuring
surface strains, cannot be read remotely, and have a lower sensitivity than the electrical
types. Repeatability depends on the skill and experience of the operator.
Pressure Cells
Purpose
Dunnicliff (1988) divides pressure cells into two general categories: (1) embedment earth
pressure cells that are installed in a soil mass, and (2) contact earth pressure cells that are
installed between a structure and a soil mass. Pressure cells are used to measure pressures
against retaining walls or tunnel linings, or stresses beneath foundations or in embank-
ments.
Device
The embedment earth pressure cell consists of a circular (or rectangular) double-wall metal
pad, and is extremely thin compared to its diameter (ratio of about 1.1 to 23 cm). A com-
mon type is the Glotzl cell, which is filled with oil or antifreeze liquid and functions
hydraulically as shown in
Figure 4.30.
Pressurized fluid is delivered to the small pressure
diaphragm by a pump or compressor until the pressure equals the resisting pressure on the
outside of the diaphragm. The diaphragm deflects a slight amount and opens a bypass ori-
fice that permits the fluid in the system to return to the reservoir. The pressure creating a
balance is read on gages that provide a measure of the external pressures acting on the cell.
One type of contact earth pressure cell used to measure loads at a pile tip or against
sheet pile wall, for example, includes a hydraulic cell with a pneumatic transducer.
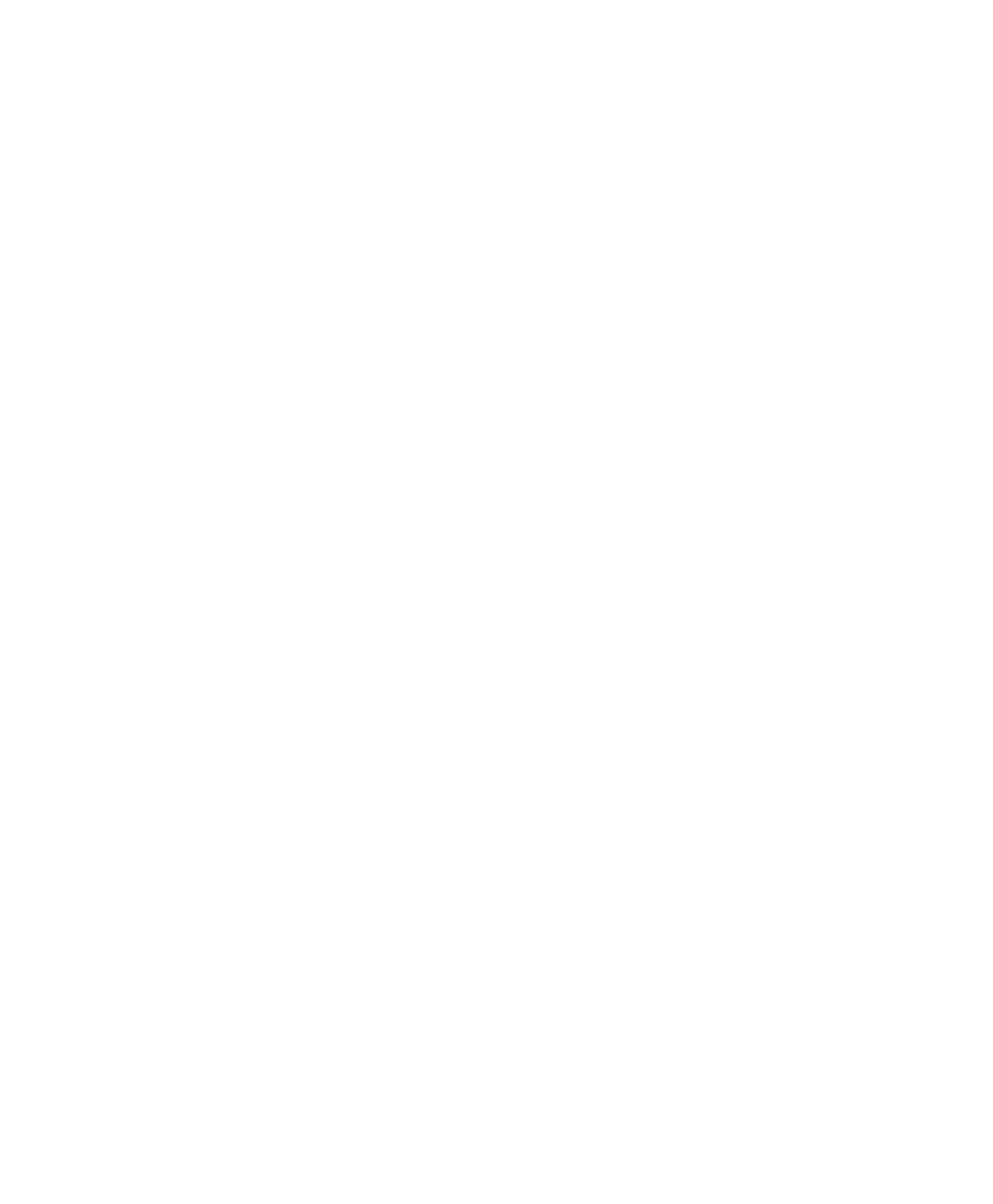