Environmental Engineering Reference
In-Depth Information
gravity, for example) will be readily and accurately obtained from the simulation. Also, the
response to any discrete gust can be examined and steps can be taken to attenuate it.
Unfortunately, the magnitude and number of turbulence cycles, whether large or small in
scale, is not well known. Wind turbine designers are therefore forced to make very
conservative (
i.e.
pessimistic) assumptions as to gust spectra, and then input these into the
simulation in order to obtain cyclic loads for fatigue life prediction. Admittedly, this will
result in an over-strength system, but the goal of achieving a design fatigue life that meets
specifications will have been realized.
Fortunately, a compliant and well-damped system will respond very little to the higher-
frequency components in a wind velocity spectrum [Stoltze 1986]. As a result, only those
temporal gusts that envelop the whole rotor need be given major attention. A major use
of the system simulator will be to evaluate the effectiveness of design features such as
teeter hinges and low-stiffness elements in attenuating responses to these large-scale gusts.
Small-scale spatial turbulence is seen by a rotating blade as a quasi-steady, periodic
series of gusts with frequencies at integer multiples of the rotor speed and amplitudes that are
inversely proportional to frequency (see Eqns. 2-35). Placing the blade flatwise frequencies
away from even multiples of the rotor speed in a teetered HAWT rotor (and all multiples
in a hingless rotor) can avoid a resonant response to these excitations. Without resonance,
the amplitudes of small-scale spatial turbulence are too small to be of design significance.
However, in actual practice, resonant frequencies can usually be crossed without a problem,
because there is sufficient damping present.
Blade Internal and External Pressures
If a hollow blade is not suitably compartmented and vented, internal air pressure or
suction caused by centrifugal force can exert design-driving loads on the shell structure.
Typically, the
afterbody
of the airfoil (
i.e.
,
the triangular section between the structural spar
and the trailing edge) with its typically lightweight construction and small curvatures can
be badly distorted with attendant material stresses that are excessive. For structural
integrity, pressure-induced stresses must be calculated and, if necessary, reduced to
acceptable levels by use of compartment walls and venting.
Optimum Turbine Size
As wind turbine design, development, and operation progress in machines of a wide
range of diameters, it will become clearer whether or not there is a diameter that is in any
way “optimum.” Land utilization costs have favored larger size, while transportation and
installation costs have favored smaller size. Meanwhile, design concepts and simulations
of system dynamic behavior have not been pushed to the degree of perfection that would
enable one to predict a rotor diameter at which economic performance may eventually
become optimized. What is clear is that the trend in the sizes of wind turbines installed in
wind power stations has been and continues to be steadily upward.
In searching for an optimum or desirable rotor diameter, it seems that one should
explore the effects of size upon
prototype
turbine systems that are in other respects most
promising. Such wind turbines would be those with high energy-capture performance and
low fatigue loading. Under these criteria, it can be informative to look at size effects in a
two-bladed HAWT with a teetered rotor, which embodies the soft-system design philosophy.
This baseline design would be presumed to operate with fixed pitch over a broad range of
speeds and with a yaw drive for limiting aerodynamic loads. As guidance in the
exploration of the effects of size on the economic performance of this or any other
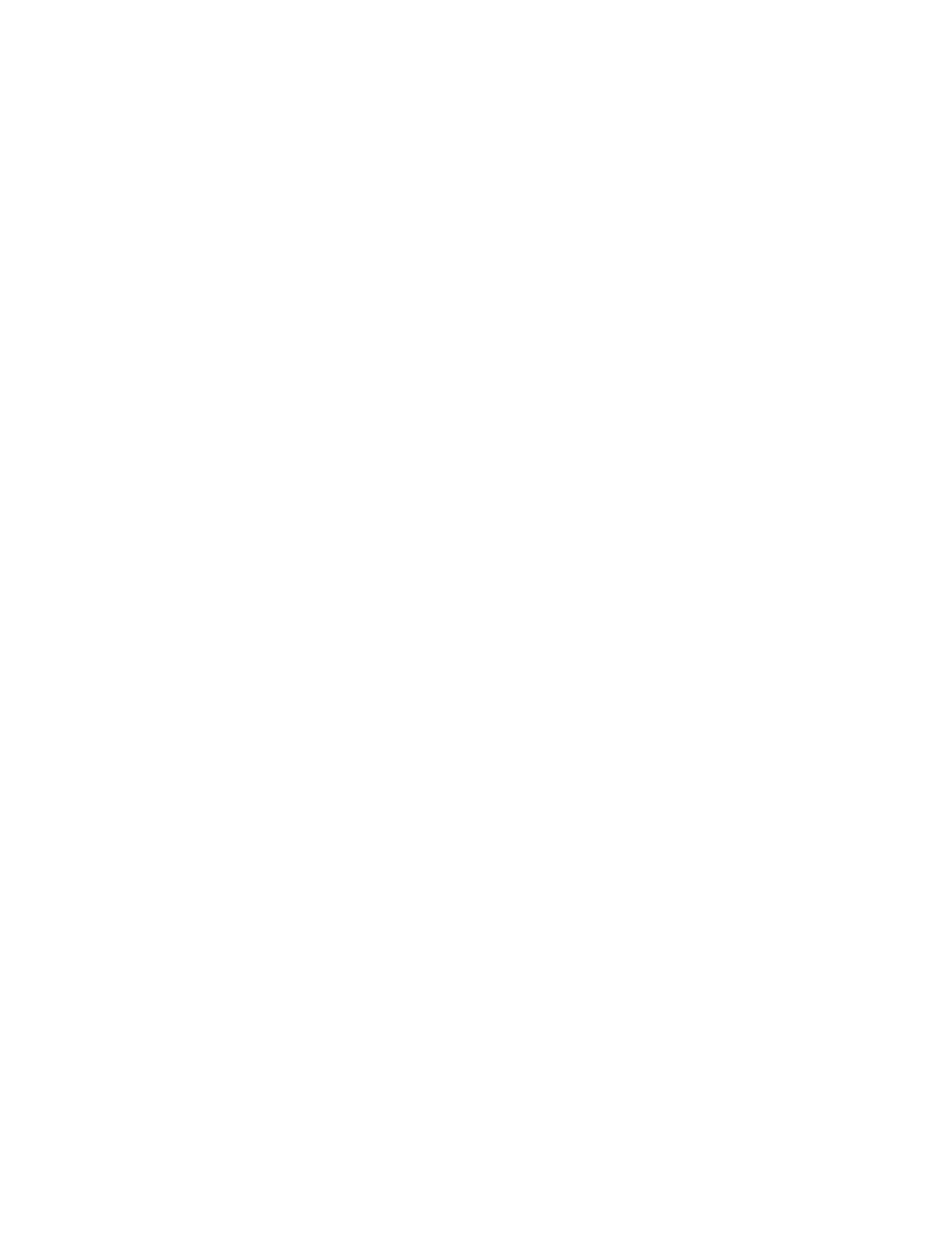
Search WWH ::

Custom Search