Environmental Engineering Reference
In-Depth Information
which converts rotary to reciprocating motion. Nominally “oilless” bronze and graphite
came to be used in later years, followed by ball and roller bearings. Lubrication does not
sound like a dificult problem, except when the bearings are on top of a tower 6 to 15 m
high, quite open to the weather. Perhaps a weekly chore of climbing the ladder and
hanging on while using the oil can or replenishing a container does not appear too risky
or arduous for a reasonably active man, but it certainly could be so during months of high
winds and icy steps in many parts of the country. Hence, there was a continuous effort to
ind better ways of reducing the need for attention to lubrication.
One of the most useful automatic lubrication devices was a canister of oil above the
bearings, normally closed at the bottom by a spring-loaded valve. A wire from the valve
down to the ground could then be pulled to release enough oil to last for a number of days,
as judged by the operator. An alternative method was to supply the tower with a hinged
center and then tilt it to permit lubrication at ground level. Raising and lowering the top
part of the tower was accomplished by using the bottom half as a derrick. A number of
hinged towers were used in the last years of the nineteenth century, but they lost favor
when they were found to be too susceptible to wind damage.
The real solution was introduced by the
Elgin Wind Power and Pump Company
,
which
enclosed bearings and other parts requiring lubrication in a casing in the manner of an
automobile crankcase. The gears carried oil up to the shaft and pinion from the case
reservoir, with feeds to the other elements of the transmission, and excess oil lowed back
to the reservoir. This served all the necessary purposes, keeping dust and water out and
eliminating splashing and loss of oil. A self-oiling mill also allowed more sophisticated
methods of transmission, such as the use of cams or worm wheels.
The Decline of the American Windmill
The production of multivane windmills was at its peak at about the time of World
War I. Although sales were still brisk in the 1920s, there were signs that their heyday
might be over. Baker attributes the decline of windmill production and sales that ensued
in the 1930s to the Great Depression, and describes it as a blow from which the industry
never recovered [1985]. The economic decline occurred throughout most of the world, and
so the very considerable export sales of U.S. companies were likewise reduced. Another
concurrent reason was that the growing demand for electricity brought power lines into the
heartland of the country. So, although times were hard, such funds as were available could
be used for electric pumps. Whatever contentment a farmer felt while listening to his
windmill working for free was apparently replaced by the ease of pressing a button to turn
on the electricity.
Sic transit gloria molini Americani.
From Windmills to Wind Turbines: 1888 to World War II
The First Wind-Powered Generation of Electricity
At the end of the nineteenth century, interest developed in using wind power for
electrical generation, particularly to service scattered habitations. According to Wolff [1885],
using a windmill to drive a generator to charge storage batteries (“accumulators”) was irst
suggested by Sir William Thomson in 1881. In his address on energy sources to the math-
ematical and physical science section (of which he was President) of the British Association
for the Advancement of Science, Sir William observed
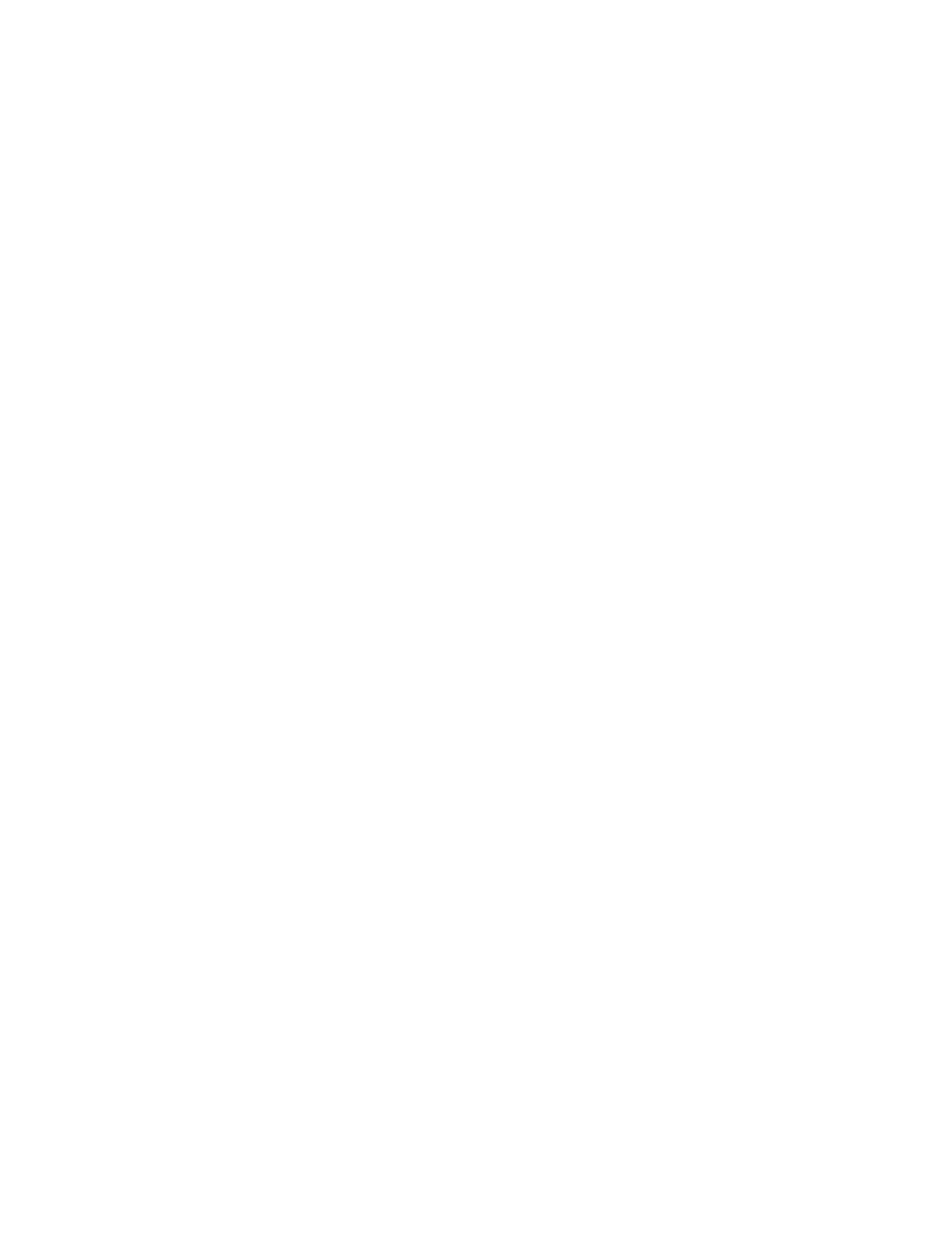
Search WWH ::

Custom Search