Environmental Engineering Reference
In-Depth Information
of 15 deg, is the region where separation and incipient stall generally commence. While
the initial stages of stall are quite sensitively connected to details of the airfoil shape, the
features of incipient stall are well-documented in the standard literature.
A basic insight into the effect of drag in the attached-flow regime on the power of a
HAWT can be obtained by taking an approach similar to that used in the fundamental
analysis of the performance of monoplane wings, that is, by calculating the ideal power
without viscous or
profile drag
losses and then estimating the power losses caused by drag
alone. A simple analysis of a constant chord HAWT rotor with a constant drag coefficient
at zero lift coefficient indicates that
d
P
V
ยป
r
Bc
W
3
R
4
8
(6-2)
C
D
,0
where
d
P
V
=
viscous power loss (W)
r
= air density (kg/m
3
)
B
= number of blades in the rotor
W = rotor speed (rad/s)
R =
rotor radius (m)
C
D,0
= drag coefficient at zero lift coefficient; profile drag coefficient
For tapered blades, the effective chord length is approximately that at about 80 percent of the
rotor radius. As an example, consider a representative small-scale turbine, the
Carter 25
HAWT shown in Figure C-2, for which
B =
2, W = 12.6 rad/s,
R =
4.9 m,
c =
0.31 m, and
C
D,0
= 0.009. This provides a representative viscous power loss of 1.0 kW at all wind speeds.
If we compare this with the rated power of 25 kW, we note that it is about 4 percent of
that value. This estimate can be refined by using a state-of-the-art rotor performance code,
taking into account details of chord and twist distributions and the air loading. When the
actual drag coefficient is reduced by
C
D,0
at all angles of attack, the improvement in power
output is predicted to be roughly constant at 1.0 kW over the operating range, which is
equal to the crude estimate above.
At a site with a typical
Weibull wind speed histogram
(Table 2-1), this represents an
8 percent energy loss from viscous effects. It should be noted that most well-sited turbines
produce the majority of their energy when operating near their maximum power coefficient,
so this energy loss estimate is accurate to a first order. For turbines generating power in
a low wind regime, energy production will be more heavily impacted by airfoil drag.
High-Lift/Stall-Development Regime
This next regime involves airfoil behavior at angles of attack from approximately 15
to 30 deg. Designers of fixed-pitch turbines pay special attention to lift and drag
coefficients in this regime, since these have a dominant effect on the peak power produced
by the rotor. Here the flow state ranges from initial incipient separation near the trailing
edge of the airfoil to massive separation over its entire low-pressure surface. The pheno-
menon of
dynamic stall
[Hibbs 1986] also takes place in this regime.
Flat-Plate/Fully-Stalled Regime
Airfoil behavior at angles of attack from approximately 30 to 90 deg is similar to that
of a simple flat plate. At 45 deg, lift and drag coefficients are approximately equal, and
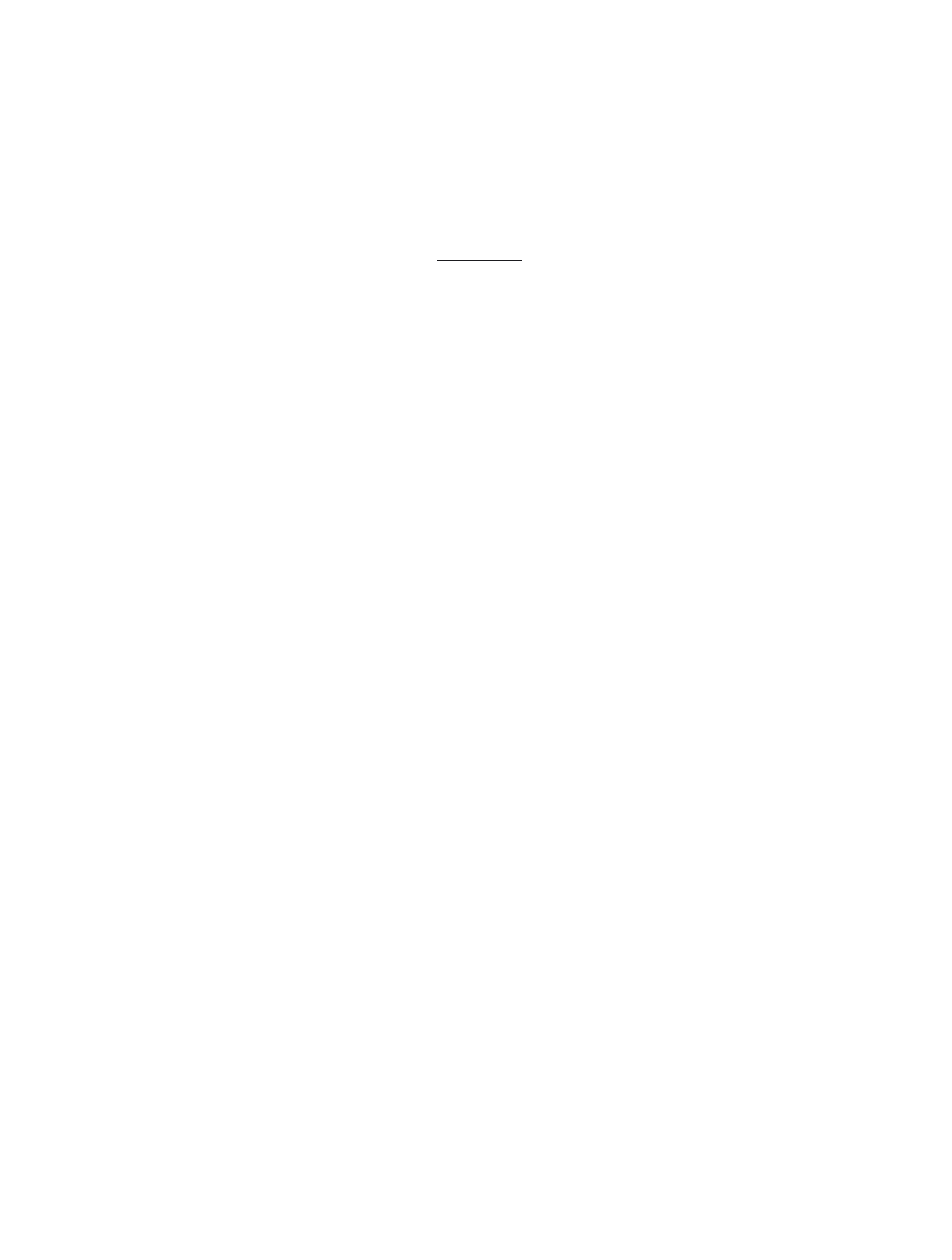
Search WWH ::

Custom Search