Environmental Engineering Reference
In-Depth Information
Aerodynamic Behavior of HAWTs in Operation
The operation of modern HAWTs includes a number of important features, such as the
use of a
teetered rotor
,
yaw response
,
aerodynamic controls
,
transient aerodynamics
, and
vortex generators
. The aerodynamic qualities of these features are discussed in this section,
along with examples of HAWT performance and aerodynamic loads.
Teetered Rotors
The rotor of an operating HAWT is continually subjected to wind conditions that cause
significant variations in the local air loads along its blades. These conditions include
wind
shear
(vertical and/or horizontal gradients in wind speed),
yaw error
(rotor disk not perpen-
dicular to the wind),
tower shadow
(reduction in wind speed caused by tower blockage),
and
small-scale turbulence
(perturbations above and below the mean wind speed over areas
smaller than the swept area).
Wind shear, for example, can cause the blade at the topmost position to experience a
higher wind speed than the blade closest to the ground. If the blade is held rigidly at the hub,
this difference in wind speed will induce a cyclic variation in local angles of attack. As a
result, each blade will experience
cyclic flatwise bending
(also called
flapwise
or
out-of-plane
bending), with a dominant frequency of once per rotor revolution or
1P
. Similar cyclic load-
ing at a 1P frequency occurs with yaw error. The effects of tower shadow and turbulence are
more complex, causing significant fluctuations in the aerodynamic loading on the blades not
only at the
1P
frequency but also at higher harmonic frequencies (
i.e.
2P
,
3P
, etc.).
Cyclic flatwise bending moments on the blades of a two-bladed HAWT are greatly re-
duced by allowing the rotor to oscillate like a see-saw about a
teeter axis
or
teeter hinge
through the outboard end of the turbine shaft, as illustrated in Figure 5-18. The teeter hinge
prevents unbalanced out-of-plane aerodynamic loads from being transmitted to the turbine
shaft, while still allowing in-plane torque loads to be carried. The effectiveness of teetering
in reducing blade bending loads can be shown by the following analysis.
Figure 5-18. Schematic diagram of a teetered, two-bladed HAWT rotor.
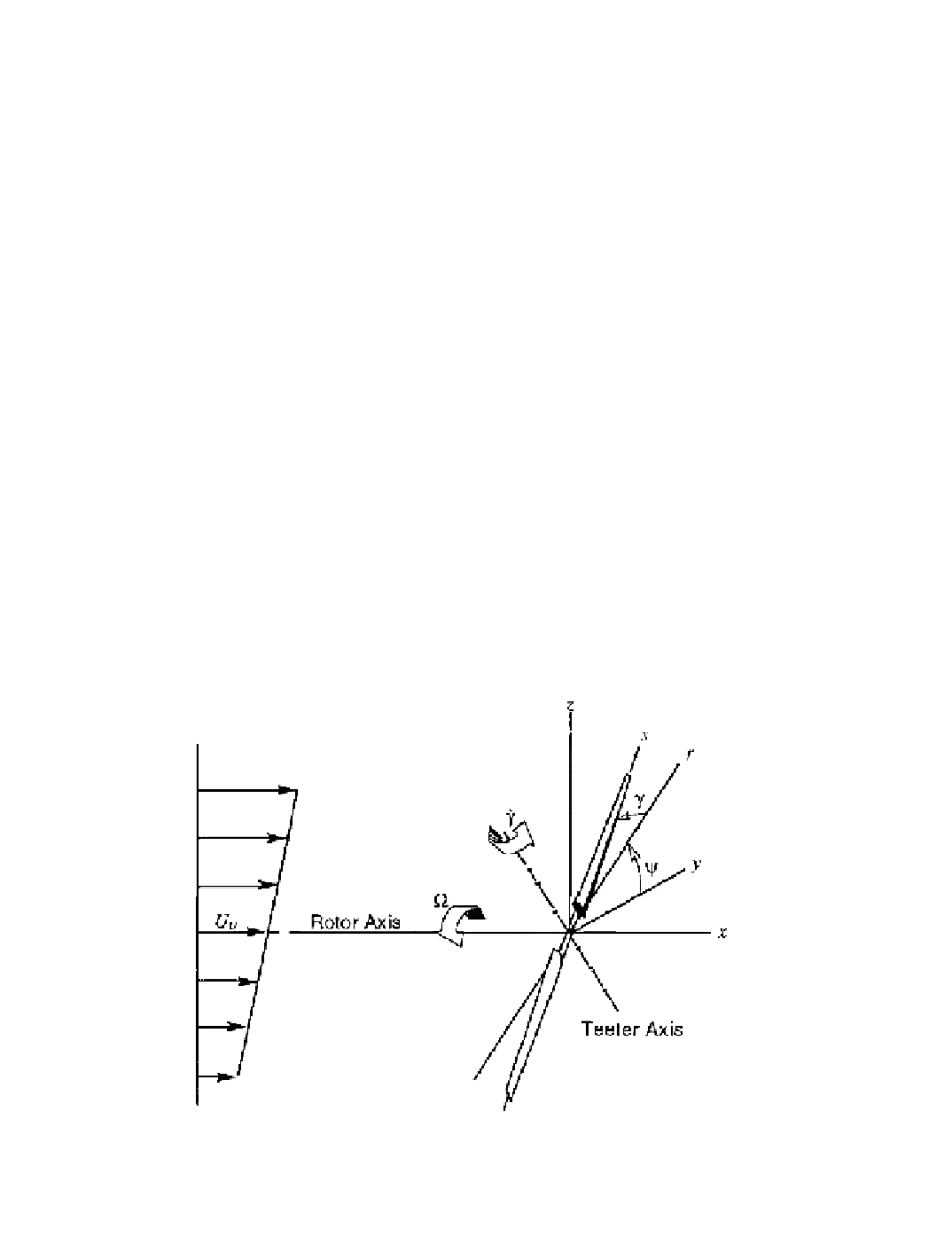
Search WWH ::

Custom Search