Environmental Engineering Reference
In-Depth Information
Tower Transportation
Towers are primarily made of rolled steel with the primary restriction for transport over
land being tower diameter. In most countries, tower diameters are limited to 4 to 4.5 m. In
countries that are mountainous, the restrictions can be less than 4 m.
The
Repower R5M 5 MW
turbine in Germany (see Fig. 2-4), with a 6 m diameter at the
tower base, demonstrates the criticality of the transportation issue facing the large wind tur-
bine industry. Large-scale towers are typically manufactured in 20 to 30 m sections because
of limits on both size and mass. Because of these constraints, it does not pay to transport
towers more than ,000 km, so they are often manufactured locally for large installations and
regional markets. Assembly costs also rise rapidly with tower height, due in part to limita-
tions on the availability of very large cranes and other construction equipment. For this rea-
son, the rental of the crane is the largest cost of assembly and erection. A 300-ft crane with
necessary 200 ton capacity can cost as much as $80,000 per day. Weather-related or other
delays can often add 0 percent per day to these costs.
As discussed earlier, medium- and small-scale wind turbines often use towers that can be
assembled from relatively small pieces. Some are assembled while horizontal on the ground
and then tilted up for installation back to horizontal for maintenance and repair. Offshore
installations can be done with jack-up barge mounted cranes (barges with retractable legs).
Assembly in ship yards and transport can be on barges, virtually eliminating weight and
height restrictions.
Water-Pumping Wind Turbines
Uses of water-pumping wind turbines include land
irrigation
, human or livestock
water
supply
, and
drainage
. Pumping water with wind power requires the rotor to deliver higher
torque than that required by an electrical generator of the same rated power. Prior to the 9th
century development of
back gearing
(speed reduction), torque requirements were particu-
larly high when one revolution of the rotor completed one pump cycle.
Designs of water-pumping windmills and wind turbines reflect their application, de-
pending on the
flow required
, the type of
well
, and the
head
(the distance from the well water
to the outlet). In the United States, most of these applications are
low flow
(approximately
m
3
/h) and
medium head
(from 5 to 45 m). In the developing world, the flow desired may
be similar, but the head is often less. The windmill may be driving a
piston
,
air-lift
, or
dia-
phragm pump
.
American Windmills
Because the demand for water is most critical during the dry or summer season, water-
pumping windmills must function when the winds are light. Most builders of water-
pumping windmills began to solve this problem by using rotors with
multiple blades
,
consisting of many flat panels or paddles placed around either a vertical or horizontal
axis (see Fig. -7). The result was the appearance of the machine known as the classic
American windmill
, a much-copied design that is now found commercially throughout the
world. The abundance of non-U.S. manufacturers of water-pumping wind machines, es-
pecially in Australia, has led some outside the United States to describe the design today
as a
classical windmill.
For pumping small amounts of water in flat terrain, no substitute has been found for the
classical, multi-bladed American
windmill driving a mechanical pump. However, when the
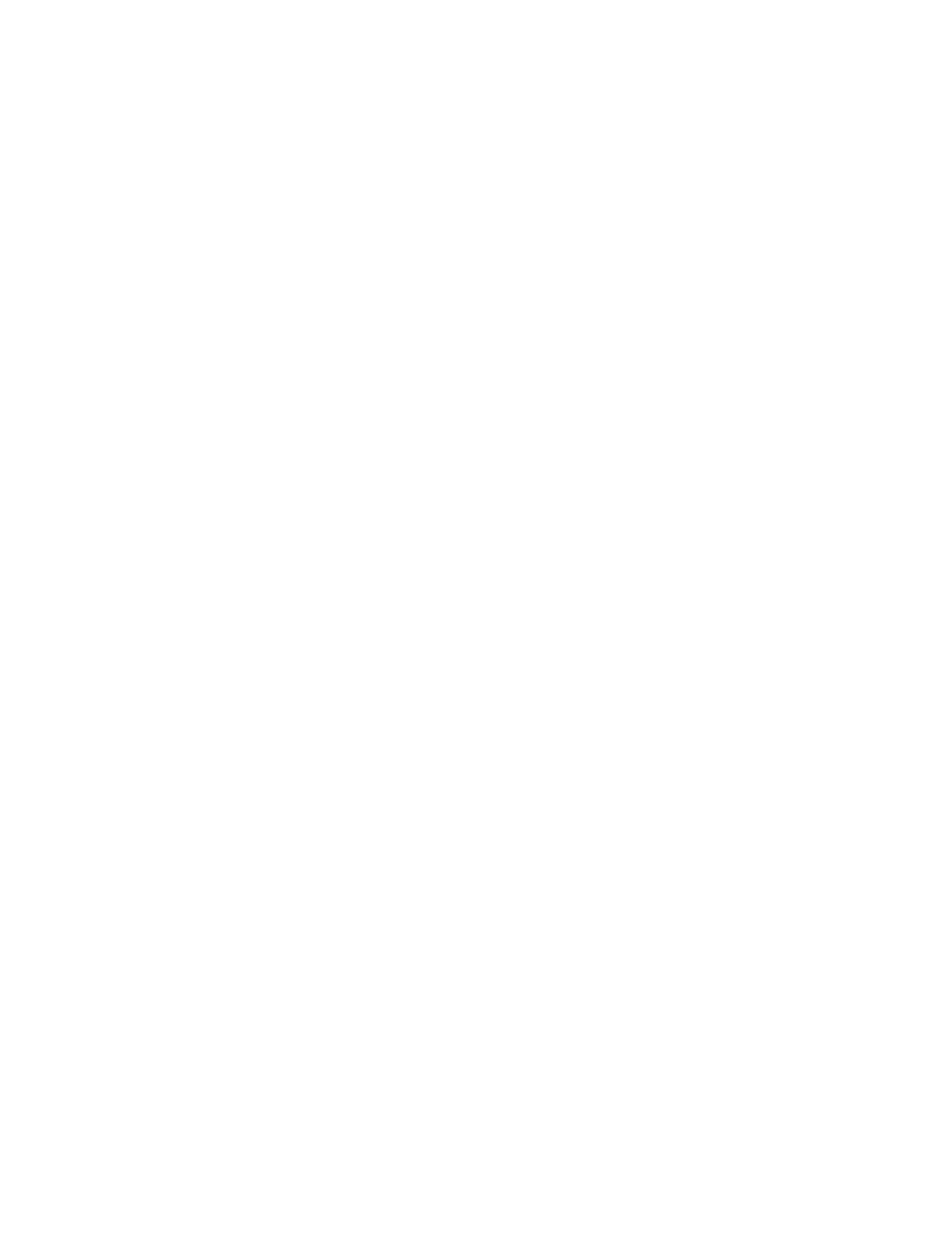
Search WWH ::

Custom Search