Environmental Engineering Reference
In-Depth Information
drivetrain project has developed a prototype for such a drivetrain that was brought to practice
by
Multibrid Gmbh
. This design uses a single-stage planetary drive operating at a gearbox ratio
of 9.16:1. This gearbox drives a 190 RPM, 72-pole, permanent-magnet generator. This design,
which reduces the diameter of a 1.5-MW generator to 2 m [Bywaters
et al.
2004], was fabri-
cated and then tested on the dynamometer at NREL's National Wind Technology Center.
Distributed Drivetrains
Another approach that offers promise for reduced size, weight, and cost is the distributed
drivetrain. This concept is based on splitting the drive path from the rotor to power several
parallel generators. Studies have shown that by distributing the rotor torque on the
bull
gear
(the main gear attached to the rotor shaft) over a number of parallel secondary
pinions
,
signiicant size and weight reductions are achieved. Figure 3-46 shows a 2.5-MW prototype
distributed power train [Clipper Windpower 2006] that is currently installed in Clipper Lib-
erty wind turbines. The development of new technology of this type and incorporation of that
technology into production wind turbines requires signiicant R&D resources and a number
of years to ensure a reliable production product.
Figure 3-46. An example of a distributed power train, in which the turbine rotor torque
(center shaft) is split among four generators.
[
Courtesy of Clipper Wind Power, Inc.
]
Towers
For the large turbines deployed since 2000, the tower coniguration used almost exclu-
sively has been a steel monopole tower on a reinforced-concrete foundation that is custom
designed according to local site conditions. The major tower variables are its height and base
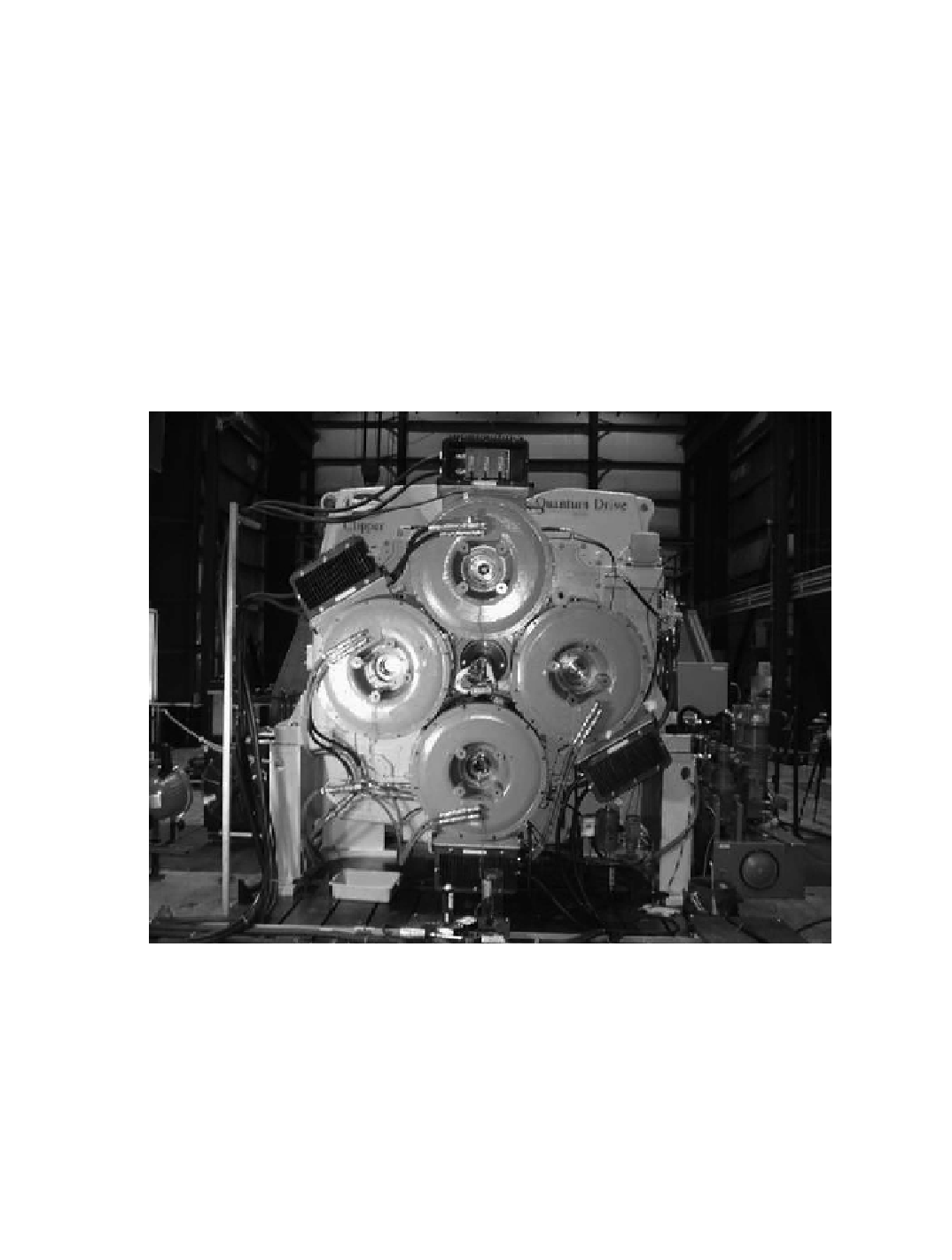
Search WWH ::

Custom Search