Environmental Engineering Reference
In-Depth Information
As turbines grow larger and larger, rotors must improve their ability to handle large
dynamic loads with increased structural eficiency to avoid the costly cubic-rule of weight
growth described previously. Today's blade designs are subjected to rigorous evaluation us-
ing the latest computer analysis tools that remove excess weight. Designers are also applying
lighter and stronger carbon iber in highly stressed locations to stiffen the blade and improve
fatigue resistance while reducing blade weight. However, carbon iber must be used judi-
ciously, because its cost is about 10 times the cost of iberglass.
Another approach to reducing the relative cost of larger rotor blades involves develop-
ing new blade airfoil shapes that are much thicker at the root where the blade needs the most
strength. In general, thin streamlined structures like airfoils are very ineficient at carrying
structural loads applied to their upper and lower surfaces. The design challenge is to make
a thick, structurally eficient airfoil cross-section that doesn't give up much in aerodynamic
performance. Figure 3-44 illustrates such an airfoil shape, called a
lat-back thick airfoil
,
which is used near the root of the blade where aerodynamic performance is less important
[Berg and Zayas 2008]. An additional beneit is that blades with this type of shorter root
chord are more easily transported over the highway, where width and height restrictions
apply.
Figure 3-44. A lat-back thick airfoil shape with high structural eficiency and moder-
ate aerodynamic performance for use in the root sections of large rotor blades.
The
relatively short chord of this cross-section also allows for easier highway transport. [Berg
and Zayas 2008]
Reducing Fatigue Loads
Another approach to increasing blade length while restraining the weight and cost growth
is to reduce the fatigue loading on the blade. There can be a big payoff in this approach be-
cause the approximate rule of thumb for iberglass blades is that a 10 percent reduction in
cyclic stress can provide about an order of magnitude increase in fatigue life. Blade fatigue
loads can be reduced by controlling the blade's aerodynamic response to turbulent wind in-
puts. This is done by using the turbine control system to continuously adjust the blade pitch
in response to luctuating winds. This approach is now being explored using modern
state-
space control strategies
so that future wind turbines can take advantage of this innovation
[Wright and Fingersh 2008].
An elegant concept for increasing blade fatigue life is to build a passive means of reduc-
ing cyclic loads directly into the blade structure. By carefully tailoring the structural proper-
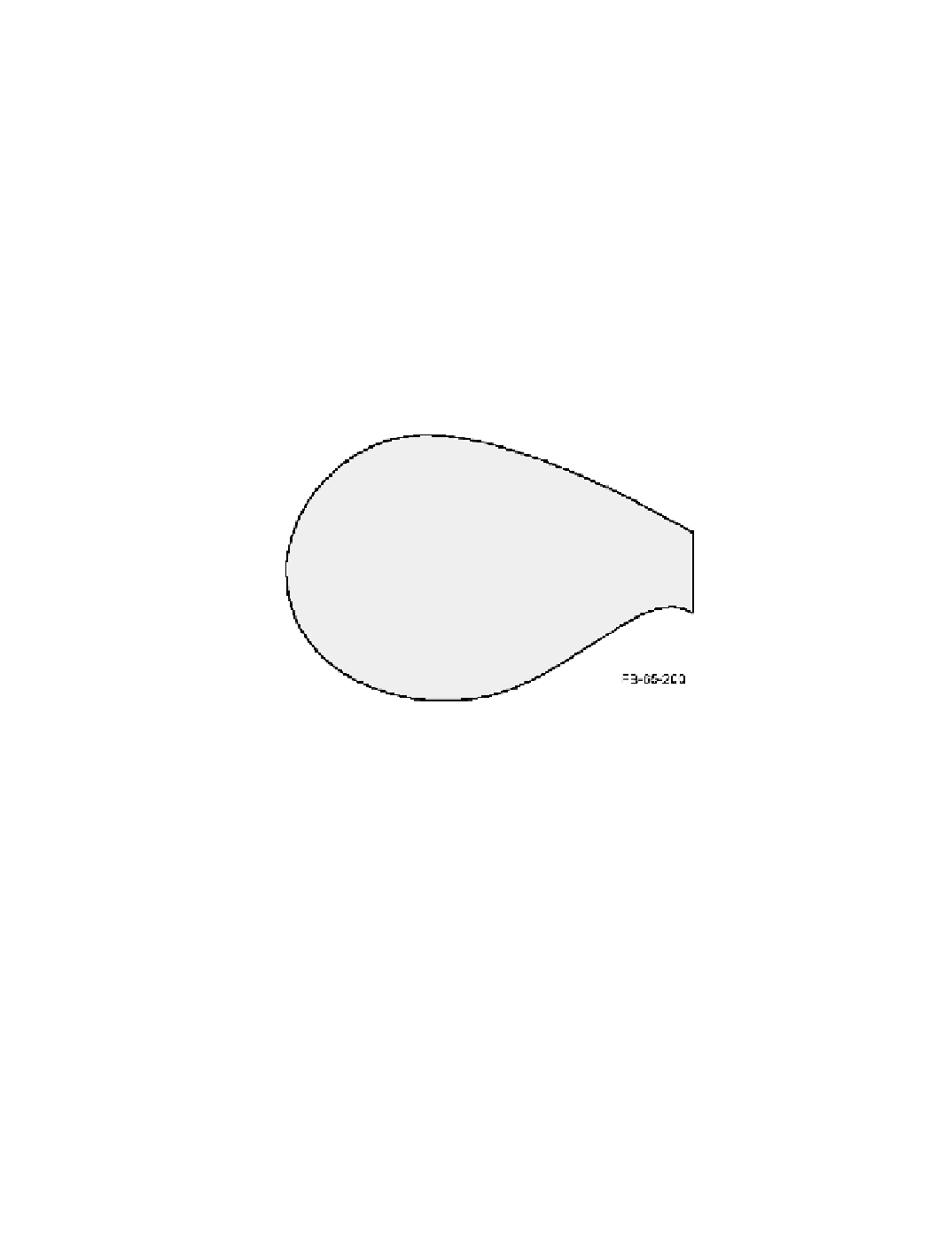
Search WWH ::

Custom Search