Environmental Engineering Reference
In-Depth Information
FIGURE 6.22
Pier foundation, concentric cans, for 3 MW wind turbine.
For those wind turbines with downwind rotors, there is a reduction of wind speed due to tower
shadow, and there will be a cyclic driving force. One aspect is the generation of noise as the blades
pass behind the tower, a repetitive sound. Repetitive sounds are more annoying than the normal
chaotic noises generated be the passing wind. For most wind turbines the noise level attenuates to an
acceptable level not too far from the wind turbine. However, the MOD-1, a downwind unit, emitted
low-frequency sound waves, and under certain atmospheric conditions, the noise was at unaccept-
able levels at considerable distances from the turbine. It was strong enough to shake the dishes on
the shelves of some homes. The solution was to reduce the rotor speed (less power), which required
the replacement of the generator.
6.9 EVOLUTION
Since 1970 the design of modern wind turbines evolved from two different ends, utility-scale, large
wind turbines and small wind turbines. The large wind turbines were primarily funded by govern-
ments, and only prototypes were built and tested, while the small wind turbines were built in large
numbers by private manufacturers for the emerging commercial market.
In the United States, NASA-Lewis began with the MOD-O design, a two-blade, downwind tur-
bine, 100-200 kW, which progressed to the design of the MOD 5, a two-blade, 7,000 kW unit. This
design was reduced to 3,200 kW, and one prototype was built, which had steel blades with teetered
hub, upwind, tip pitch control. The tip pitch control was driven by motors in the blades, which made
maintenance a problem. The Hamilton-Standard WTS-4 was a 4,000 kW wind turbine with two
blades, downwind, pitch control, and teetered hub.
The Schachle-Bendix wind turbine had an interesting concept: a variable-speed, hydraulic drive
in the power train, which was connected to hydraulic drives on the ground to drive the generator.
The losses in the hydraulic drive were high, and the unit only reached a power output of 1.1 MW
rather than the designed 3 MW. The unit was mounted on a tripod trust tower, which rotated on a
track, so the tower was yawed for control.
In Europe several large prototypes were built. In Denmark the wind turbines were the Nibe A and
Nibe B, three blades, upwind, 630 kW, fixed-pitch blades for A and variable-pitch blades for B; Tvind,
three blades, variable pitch, upwind, 2,000 kW; and Tjaereborg, three blades, upwind, 2,000 kW. In
Sweden four 2,000 to 3,000 kW wind turbines were built. One had an angle gear drive to the genera-
tor in the top of the tower, so slip rings were not needed for the transfer of power. A second unique
feature was a carriage assembly on rails on the side of the tower to raise and lower the entire assembly,
nacelle and rotor. In Germany the largest wind turbine was the Growian I, two blades, variable pitch,
downwind, 3,000 kW. Other megawatt prototypes were built in Italy, the Netherlands, Spain, and the
United Kingdom. The largest VAWT was built in Canada, a 4 MW Darrieus unit.
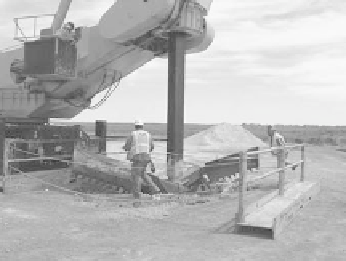
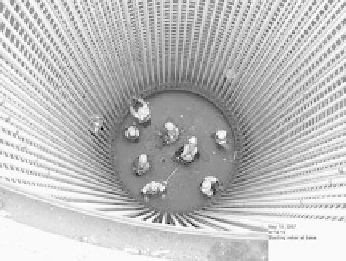
Search WWH ::

Custom Search