Geology Reference
In-Depth Information
SIDEBAR 7.5 CONVENTIONAL BOILERS AND FLUIDIZED-
BED BOILERS
The largest plant In the world burning fine coal waste from a
preparation plant is in France. The plant includes both a conventional
boiler and a fluidized-bed boiler with a total capacity of 1,200 megawatt of
electricity. The conventional boiler is fed by an 8 percent moisture vacuum-
filtered material from the preparation plant, while the fluidized-bed boiler is
fed by a fine coal slurry from the preparation plant and old slurry
impoundments (Couch, 1998). The slurry burned by the fluidized-bed
boiler contains 33 percent water, 30 percent or more ash, and a high clay
content, which makes it difficult to dewater further.
The EPA reviewed the hazards of disposal of coal combustion waste,
including that from fluidized-bed combustion, and concluded that these
wastes should retain their exemption from hazardous waste regulations
under the Resource Conservation and Recovery Act. The EPA also
concluded that additional regulations for non-hazardous solid waste
should be implemented under Subtitle D of Resource and Conservation
and Recovery Act (EPA, 2000). The fluidized-bed coal combustion waste
generally did not leach metals or toxic compounds, but the use of fluidized-
bed combustion wastes for mine reclamation warrants further review
because of possible groundwater consequences (EPA, 1999).
the water in the slurry generating the steam (J.Morrison and B.Miller,
Pennsylvania State University, personal communication, 2001).
Low-value coal can be used but must be accommodated in the initial
system design. Additional research and operational experience will be required
to specify the coal property requirements for the different types of gasifiers
(Rousaki and Couch, 2000). High-ash and low-moisture coals perform best in
moving-bed gasifiers, in which the temperature differentials permit localized
melting of ash, which can then be removed as slag. Fluidized-bed gasifiers do
not handle ash well; but in entrained-flow gasifiers, ash can be converted to slag
by adding a fluxing agent.
Barriers to the integrated gasification combined cycle process include high
capital cost and lower reliability than operators currently require (Rousaki and
Couch, 2000). These barriers reflect the complexity of process designs and
limited operational experience. All U.S. integrated gasification combined cycle
plants have been subsidized by the government, as they have in Spain and
Germany. In addition, to produce 800 megawatts of electricity, the turbines and
gasifiers must be in parallel trains, introducing a size limitation.
Despite these challenges, seven integrated gasification combined cycle
plants are in use. Three in the United States (Florida, Indiana, and Nevada)
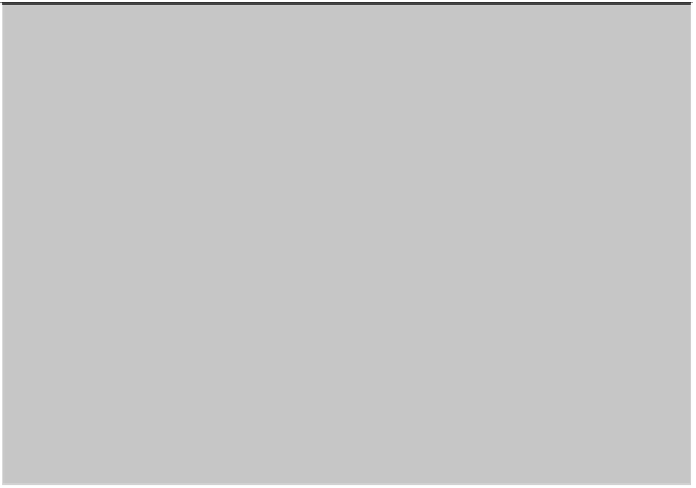





Search WWH ::

Custom Search