Civil Engineering Reference
In-Depth Information
option) allows a nonlinear stress-strain curve to be used (see Section 5.4.2 of
Chapter 5
in this topic). The first part of the nonlinear curve represents the
elastic part up to the proportional limit stress with Young's modulus of (
E
)
200 GPa and Poisson's ratio of 0.3 that were used in the finite element
model.
The developed finite element model for the composite plate girder G1
(see
Figure 7.2
) was verified against the test results detailed in Ref. [
7.29
]
.
The failure loads, failure modes, and load-midspan deflection curves
obtained experimentally and numerically using the finite element model
were compared. The deformed shapes of composite plate girder G1 at failure
observed numerically are shown in
Figure 7.3
, which is in good agreement
mode observed experimentally and confirmed numerically was combined
steel yielding (SY) in the bottom flange of the steel plate girder and concrete
crushing (CC). The data obtained from ABAQUS [1.29] have shown that
the von Mises stresses at the maximum stressed fibers at the bottom flanges
at midspan exceeded the measured yield stress as well as the stresses in
the concrete slab at midspan reached the concrete compressive strength.
In
Figure 7.4
,
the stress (principal stresses in direction 2-2) contours at failure
of the composite plate girder G1 are plotted. It can be seen that the yield
stresses were reached at midspan in the concrete (compressive stresses with
negative sign) and lower steel plate girder flanges (tensile stresses with pos-
itive sign). In addition, in
Figure 7.5
, the plastic strain (principal strains in
direction 2-2) contours at failure of the composite plate girder G1 are
Figure 7.3 Deformed shape at failure of composite beam G1 (enlarged 10 times).
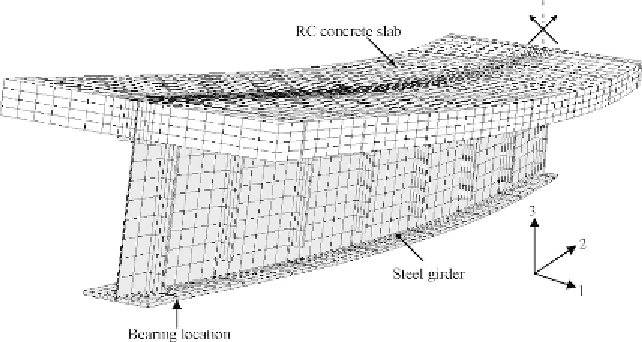
Search WWH ::

Custom Search