Civil Engineering Reference
In-Depth Information
A
P/2
P/2
1500 mm
600
1500
A
(a)
Elevation
200 mm
900
6
(b)
Cross-section A-A
Figure 6.1 General layout of a small-scale plate girder in bending (T1).
started to buckle. The yield stress estimated from the test T1 was 1809micro-
strain, which corresponded to a yield load of 1474 kN. The maximum
applied load in the bending test was nearly equal to this yield load. This means
that the bending strength of T1 model was almost the same as the yield
moment. The load-midspan deflection relationship, load-strain relation-
ships, and the deformed shape at failure were observed in the test. The upper
flange buckled between the two loading points. The web was also deformed
outward so that the web and the flange remained perpendicular. This defor-
mation shows a typical torsional buckling shape of the plate girders.
To model the small-scale plate girder (T1) tested by Nakamura and
model has accounted for the measured geometry, initial geometric imper-
fections, and measured material properties of the plate girder. Finite element
analysis for bucking requires two types of analyses. The first is known as
eigenvalue analysis that estimates the buckling modes and loads. Such anal-
ysis is linear elastic analysis performed with the load applied within the step.
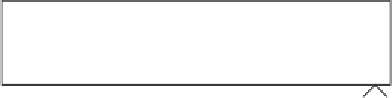

































Search WWH ::

Custom Search