Civil Engineering Reference
In-Depth Information
N
A
¼
3,327,200
150
800
¼
27
:
73MPa
M
x
I
x
y ¼
89,784,750
150
800
3
12
400
¼
5
:
61MPa
=
M
y
I
y
x¼
262,350,000
800
150
3
12
75
¼
87
:
45MPa
=
f
max
¼
27
ð
:
73 + 5
:
61 + 87
:
45
Þ ¼
120
:
79MPa
<
340MPa Then O
ð
:
K
:
Þ
4.3 DESIGN EXAMPLE OF A THROUGH TRUSS HIGHWAY
STEEL BRIDGE
The second design example presented in this chapter is for a through truss
highway steel bridge (
Figure 4.35
)
. The general layout of the through bridge
is shown in
Figures 4.36
and
4.37
,
with a brief introduction to the bridge
components previously explained in Figure 1.21. This type of trusses is a
Pratt truss bridge first designed by Thomas and Caleb Pratt in 1844. A Pratt
truss has parallel top and bottom chords and is an efficient form of a truss
arranged such that long diagonals are subjected to tension and verticals in
compression. The truss bridge has simply supported ends with a length
between supports of 60 m. The truss bridge has an N-shaped truss with
10 equal panels of 6 m. It is required to design the bridge adopting the design
rules specified in EC3 [1.27]. The steel material of construction of the bridge
conformed to standard steel grade EN 10025-2 (S 275) having a yield stress
of 275 MPa and an ultimate strength of 430 MPa. The dimensions and gen-
eral layout of the bridge are shown in
Figures 4.36
and
4.37
.
The bridge has
upper and lower wind bracings of K-shaped truss members. The expected
live loads on the highway bridge conform to Load Model 1, which
4
4
6
16.5
28 cm
14
7.5
4
Figure 4.35 The designed roller and hinged line rocker fabricated steel bearings.







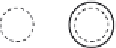
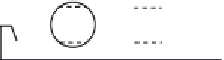


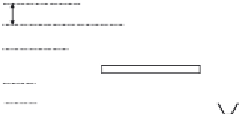


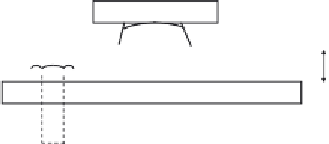

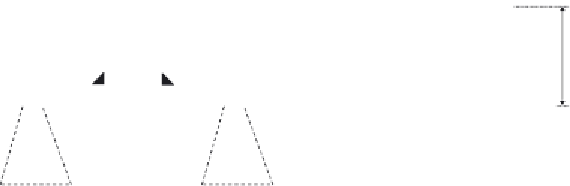
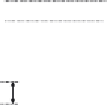









































Search WWH ::

Custom Search