Civil Engineering Reference
In-Depth Information
Socket
Figure 3.46 Detailing of hinged line rocker-fabricated steel bridge bearings.
When designing a line rocker, the maximum eccentricity of the reaction
(due to the restraining torque that the bearing provides) needs to be consid-
ered carefully (there is no tensile restraint at the line of contact).
3.11.4 Design Rules for Bearings
The current technical specifications for designing different bearings are
given in EC3 (BS EN 1993-2) [1.27]. The code gives guidance for designing
covered by the code, which are bearings that transmit moments as a primary
function, bearings that resist uplift, bearings for moving bridges, bearings for
concrete hinges, and bearings for seismic devices. According to the code
[1.27], hinged (fixed) bearings prevent movements but other bearings such
as guided bearings allow movements in one direction while free bearings
allow movements in all directions. Detailed information on bearings is pre-
sented in 11 parts of BS EN 1337-1 [
3.11
]. Part 1 of the code provides gen-
eral design rules for bearings. Parts 2-8 cover design rules for sliding
elements, elastomeric bearings, roller bearings, pot bearings, rocker bearings,
spherical and cylindrical PTFE bearings, and guided bearings and restraint
bearings, respectively. Part 9 covers protection, part 10 covers inspection
and maintenance, and finally, part 11 provides guides on transport, storage,
and installation. According to EC3 (BS EN 1993-2) [1.27], the bearing lay-
out should be designed to permit the specified movement of a bridge with
the minimum possible resistance to such movements. The arrangement of
bearings for a structure should be considered in conjunction with the design





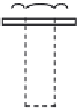


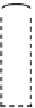

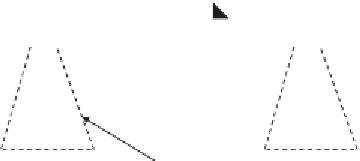
















Search WWH ::

Custom Search