Environmental Engineering Reference
In-Depth Information
Fig. 9.8 Novelty Index under unknown damaged levels
9.2.4 Experimental Example
9.2.4.1 Composite Blade and Experimental Setup
An experiment was designed to demonstrate effects of stiffening and structural
damage on the structural modal parameters. Furthermore, all modal parameters were
processed by the PCA method described above to distinguish the structural damage.
Three prototypes of 1.25-m glass fiber reinforced plastic (GFRP) composite
wind turbine blades were used in this experiment. They were mounted vertically in
the wind turbine tower. The accessories shown in Fig.
9.9
include the blades, the
ring flange, the rotating shaft, the slip ring, the wheel boss, the footstock, and
the tower. The three blades were integrated with the ring flange through bolts and
were then installed on the rotating shaft. The slip ring with 24 channels can
conduct the electric signal of the sensors on the rotating blades to fixed signal
wires, which solves the problem in which signal wires intertwine together when
the blades are rotating. The wind turbine tower is a hollow steel tube with a thick
wall that is installed on the ground with bolts. There is a cowling in front of the
wind turbine blades, which can reduce the windward resistance.
Three accelerometers, type B&K 4507B, were used for the measurement of the
vibration motion of the blades. They were attached to the tip of each blade.
According to the direction that the sensors were fixed, the acceleration signal
measured in the test corresponds to the vibration perpendicular to the rotating
Fig. 9.9 The wind turbine used in experiment
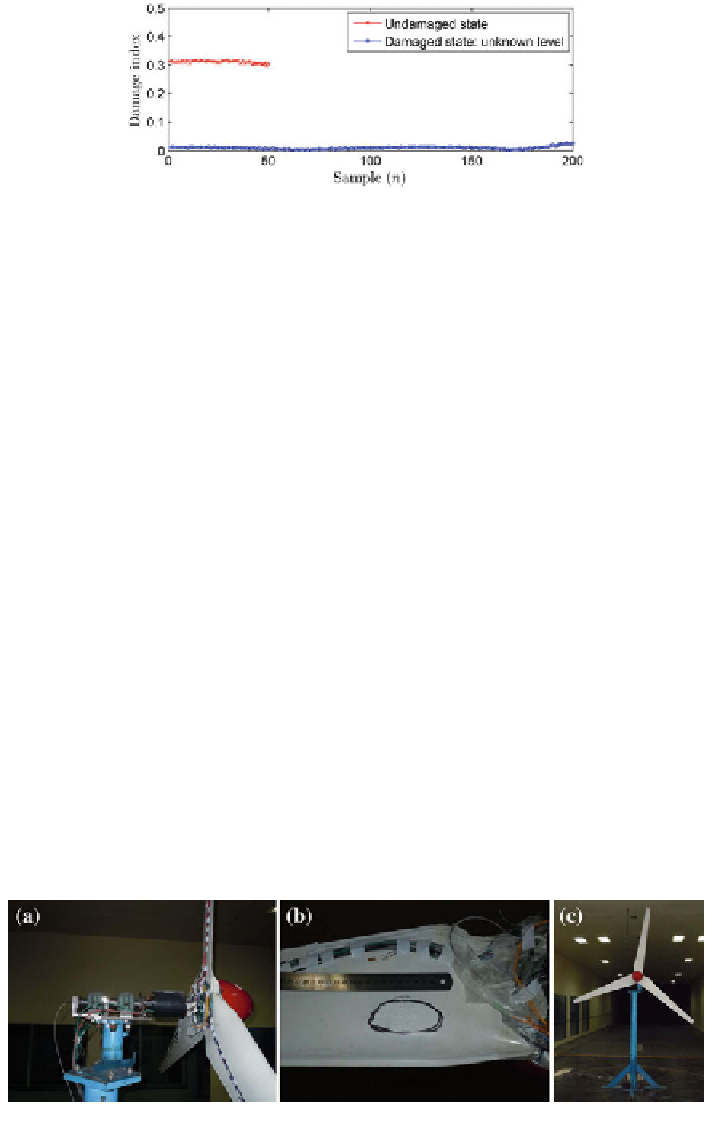