Environmental Engineering Reference
In-Depth Information
Fig. 9.3 FE model of the
wind turbine blade
of 1 rad/s, are applied within ANSYS. Thus, a total of 200 scenarios were sim-
ulated. The simulations are performed by a prestressed transient dynamic analysis
with ANSYS. The stress stiffening and large deformation effects were turned on
during the modal analysis. A high-performance computer with eight processors is
used to implement all of the simulations. Five sensors are uniformly placed on the
top side of this blade to measure the acceleration in the y direction. The sampling
frequencies for all sensors are 1,000 Hz, and 60,000 data points within 60 s are
recorded for each sensor. A typical vibration signal (y direction) is shown in
Fig.
9.3
.
9.2.3.2 Results of Modal Analysis
To verify and investigate the finite elements model and analysis considering the
rotational effects, a modal analysis was conducted prior to vibration simulation and
damage detection. Figure
9.4
shows the varying frequency of the first four modes
at different rotational speeds for both the undamaged and damaged status. This
Fig. 9.4 Varying
frequencies w.r.t. rotational
speed
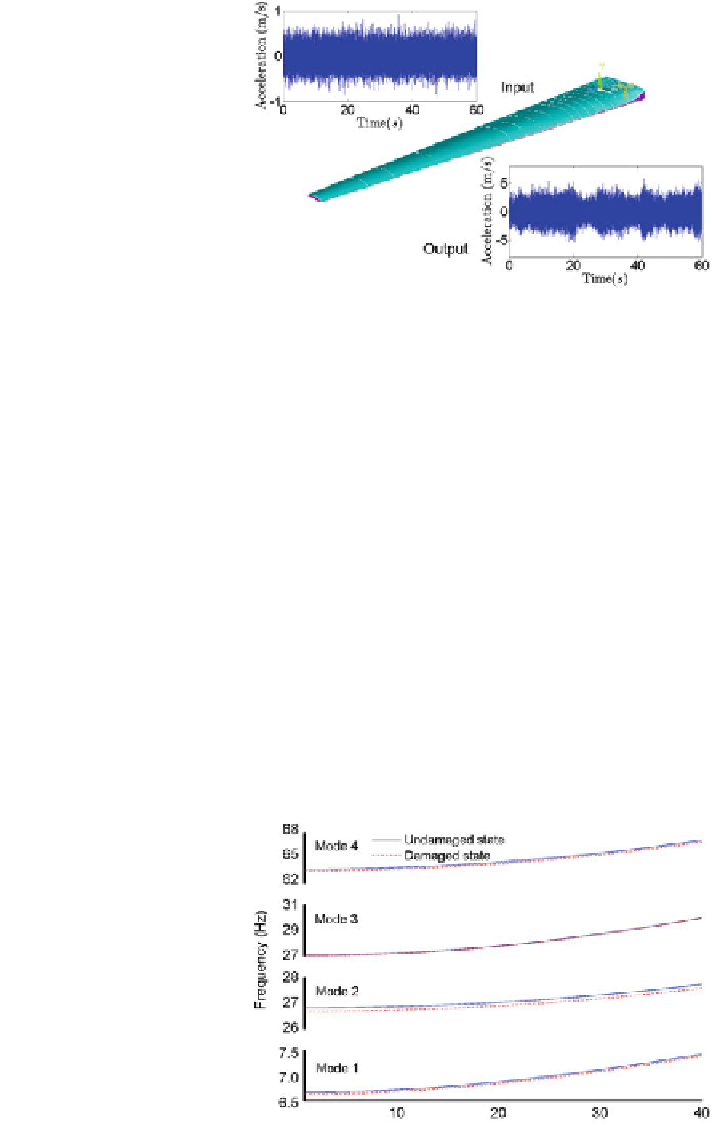