Environmental Engineering Reference
In-Depth Information
Fig. 6.6 System outputs and
blade pitch angle, sensor 3
has failed
Rotor speed
Blade 1 position
3
Full K
Diagonal K
2
Full K
Diagonal K
2
1
1
0
0
−1
−1
0
50
100
0
50
100
[Time]
[Time]
Generat
o
r speed
Blade 2
p
osition
300
Full K
Diagonal K
Full K
Diagonal K
0.5
200
100
0
0
−100
−0.5
0
50
100
0
50
100
[Time]
[Time]
Platform pitch position
Blade 3 position
2
0.1
Full K
Diagonal K
Full K
Diagonal K
0.05
1
0
0
−0.05
−1
−0.1
0
50
100
0
50
100
[Time]
[Time]
Table 6.2 c-values
c-value for full gain
c-value diagonal gain
208
6331
Simulation done with the baseline controller is also included in the figures as a
reference plot. This baseline controller comes with the FAST package and is a
gain-scheduled PI controller. The controller proposed in this chapter is individual
pitch in contrast to the baseline which is a collective pitch controller.
In order to evaluate the drive train oscillations, the standard deviation of the
speed difference between rotor—and generator—speed is calculated. The values
are normalized in such a way that the value for the baseline controller is used as
reference and given value 1, see Table
6.3
.
By using an individual pitch controller, it is possible to have a controller
which handles events such as sensor failure in a good way. That is; if one of the






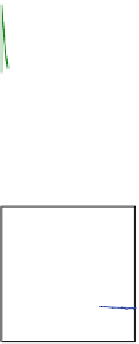




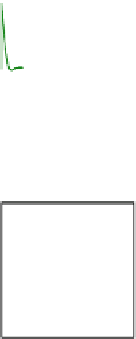
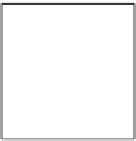







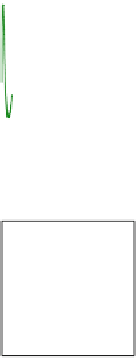





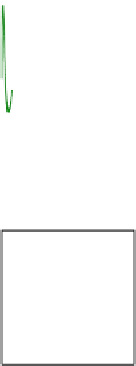
















































































































