Agriculture Reference
In-Depth Information
Virginia for hands-on sessions. In addition, the company required that U.S. en-
gineering teams make periodic on-site inspections for safety and quality control,
but these ended in 1982, when the plant decided that these costs were too high.
Instead, the U.S. contingency was responsible for budgetary and technical con-
trols but not for safety. The last U.S. inspection in 1982 warned of many hazards,
including a number that have since been implicated as contributing to the leak
and release.
From 1982 to 1984, safety measures declined, which was attributed to high
employee turnover, improper and inadequate training of new employees, and
low technical savvy in the local workforce. On-the-job experiences were often
substituted for reading and understanding safety manuals. (Remember, this was
a pesticide plant.) In fact, workers would complain of typical acute symptoms
of pesticide exposure, such as shortness of breath, chest pains, headaches, and
vomiting, yet they would commonly refuse to wear protective clothing and
equipment. The refusal in part stemmed from the lack of air conditioning in
this subtropical climate, where masks and gloves can be uncomfortable. After
1982, Indian, rather than the more stringent U.S., safety standards were generally
followed at the plant. This probably contributed to overloaded MIC storage tanks
(company manuals cite a maximum of 60% fill).
The release lasted about two hours, after which the entire quantity of MIC had
been released. The highly reactive MIC arguably could have reacted and become
diluted beyond a certain safe distance. However, over the years, tens of thousands
of squatters had taken up residence just outside the plant property, hoping to
find work or at least to take advantage of the plant's water and electricity. The
squatters were not notified of hazards and risks associated with the pesticide
manufacturing operations, except by a local journalist who posted signs saying:
“Poison Gas. Thousands of Workers and Millions of Citizens Are in Danger.”
This is a classic instance of a “confluence of events” that led to a disaster. More
than a few mistakes were made. The failure analysis found the following:
The tank that initiated the disaster was 75% full of MIC at the outset, well
above the 60% maximum recommended in the safety manual.
A standby overflow tank for the storage tank contained a large amount of
MIC at the time of the incident. Overflow tanks under normal conditions
should be empty.
A required refrigeration unit for the tank had been shut down five months
prior to the incident, leading to a three- to fourfold increase in tank tem-
peratures over expected temperatures.
One report stated that a disgruntled employee unscrewed a pressure gauge
and inserted a hose into the opening (knowing that it would do damage but
probably not to nearly the scale of what occurred).
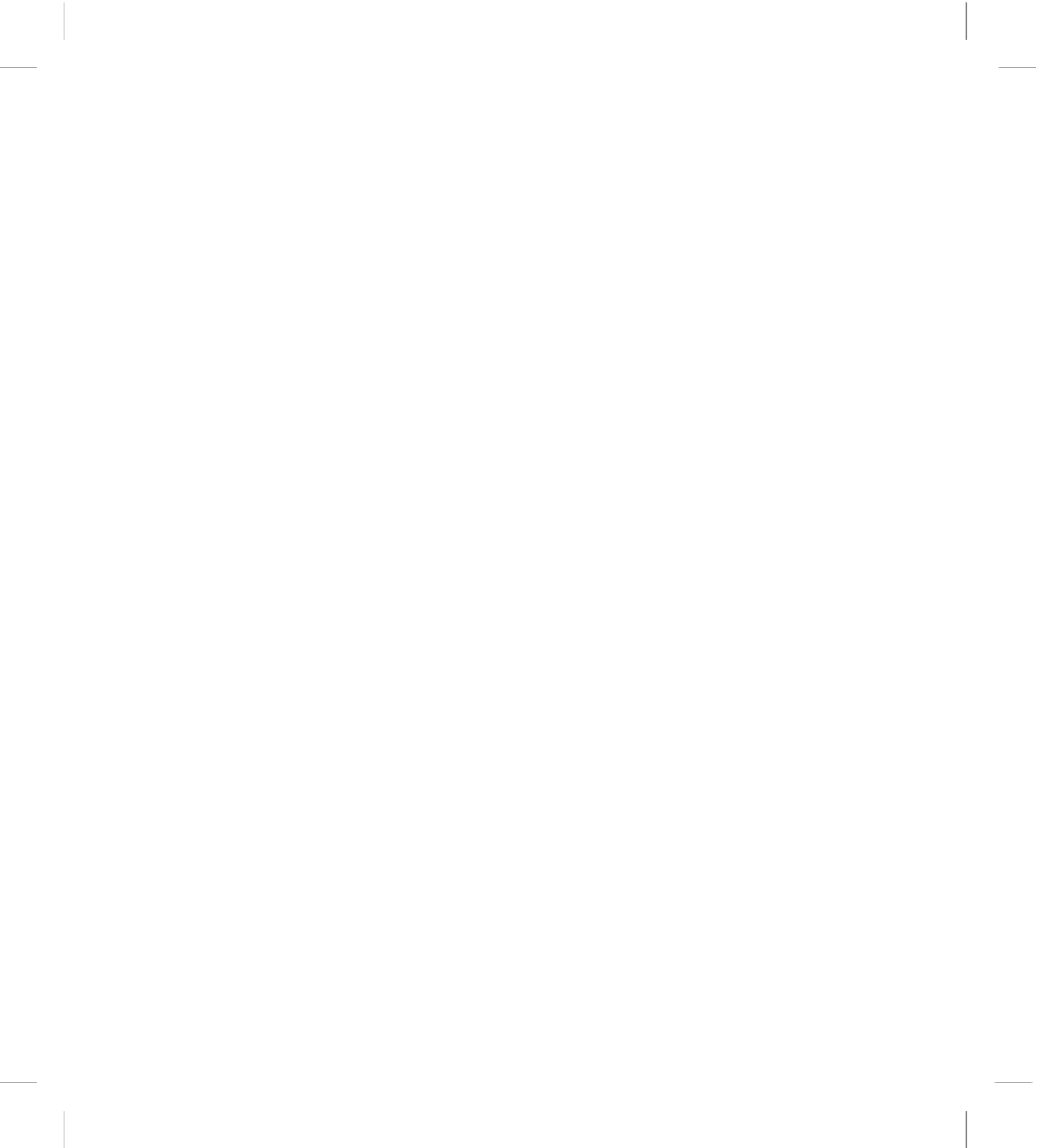
Search WWH ::

Custom Search