Biomedical Engineering Reference
In-Depth Information
thicknesses. The relationship between the tool radius and minimum chip
thickness depends on the cutting edge radius and the material of the
workpiece. This minimal chip thickness, which has been studied extensively
[44-46] can be obtained either by experiments or FE analysis (Figure 10).
Regenerative chatter presents an important phenomenon that needs to be
taken in consideration, however, accurate dynamic measurement between the
tool and the workpiece is extremely challenging [41]. It has been suggested by
various authors that chatter, tool wear, monitoring and work handling are one
of the issues that have not been sufficiently investigated on a micro scale.
Chatter presents a very significant problem due to the fact that vibrations
can have a catastrophic impact in micro systems leading to failure.
Micromachining has to incorporate two aspects of chatter, the fact that
contrary to macro machining cases, the feed rate will have an influence due to
the elasticity of the workpiece and the regenerative aspect resulting in dynamic
change of the chip thickness.
Another important issue in chatter in micro drilling is the fact that
homogeneity of the material machined cannot be assumed. In macrodrilling,
the effect of grains, grain boundaries and anisotropy of the material can be
neglected, while in microdrilling due to the size of the tool, they will have a
significant effect on the process.
Figure 10. Schematic of the effect of the minimum chip thickness (Re, radius of cutting
tool; h, undeformed chip thickness; hm, minimum chip thickness) [43].
Apart from the aforementioned problems when investigating chatter in
micromachining, there are also the issues of tool run-out caused by
misalignment of the axis of symmetry between the tool and tool holder or
spindle, available sensing methods for monitoring and controlling high speed
machining processes, thermal expansion, and the application of adaptive
control techniques.
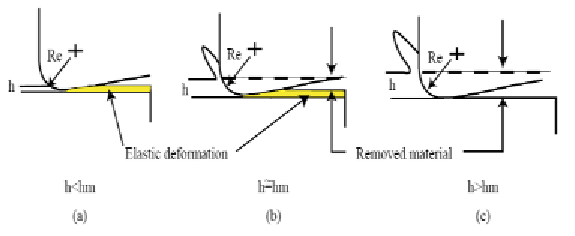
