Environmental Engineering Reference
In-Depth Information
Figure 7.8
FloatStar structure
model via the ES shell. With these tools, SGS has developed soft sensors for parti-
cle size measurements in the grinding ES installed at several concentrators. As for
FLEETâ„¢, it is a combination of methodology and software that analyzes the vari-
ability of flotation plant responses in order to improve their design and optimize
production planning.
The introduction in 1999 of a MET ES for SAG milling at Ok Tedi brought
about significant improvements in circuit throughput. In 2002 a MET neural net-
work model was developed and deployed to enhance the existing ES solution. The
main objective of this model was to predict the effect that changes in SAG tonnage
and density would have on mill power draw. The result was a decrease in process
variance with an associated increase in average circuit performance. The improve-
ment in power draw was 35% over that already obtained with fuzzy expert control
alone. This led to an additional 2% in calculated throughput on top of the 5.3%
quoted in an earlier paper [63]. An important supplementary benefit was the reduc-
tion in variability, which ultimately benefits flotation.
As regards developments in flotation, MET and JKFrothCam were installed in
80 OK-100 copper flotation cells at Escondida to control cell level and air flow.
An evaluation found that feed consistency in the cleaning circuit was improved and
recovery rose by 1.3%.
7.5 Conclusions and Trends
The foregoing review has shown that a significant number of industrial products,
including innovative sensors and tools for the development, implantation and eval-
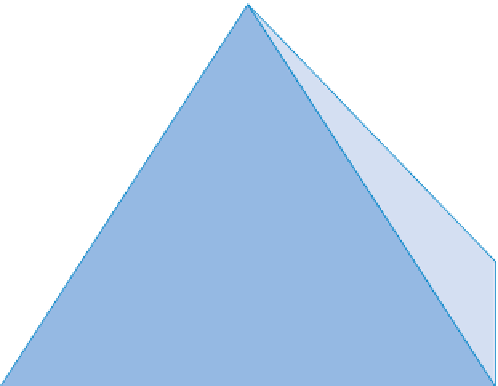

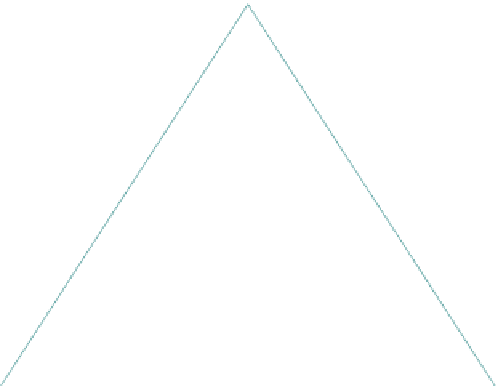
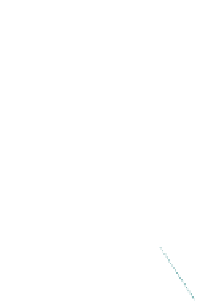


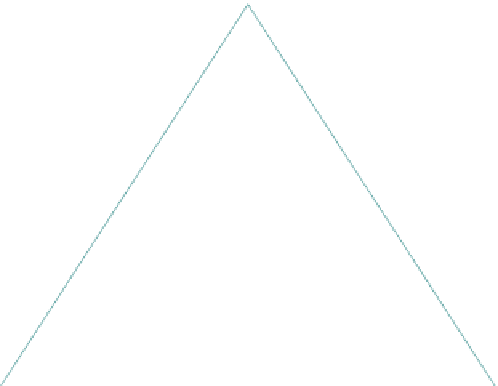



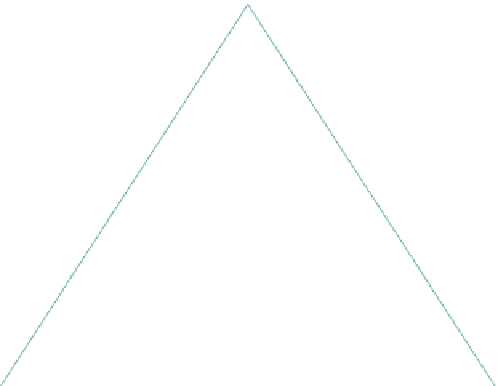




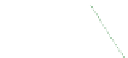
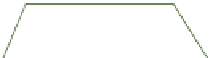

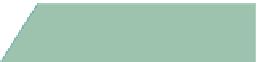



















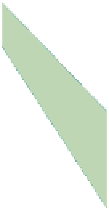


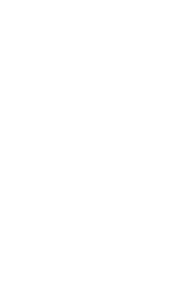















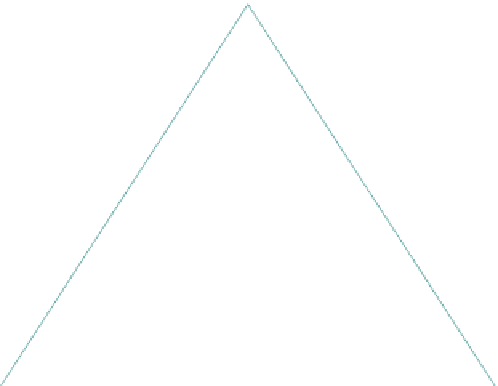


















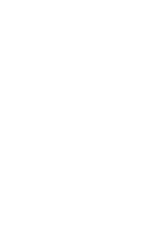


















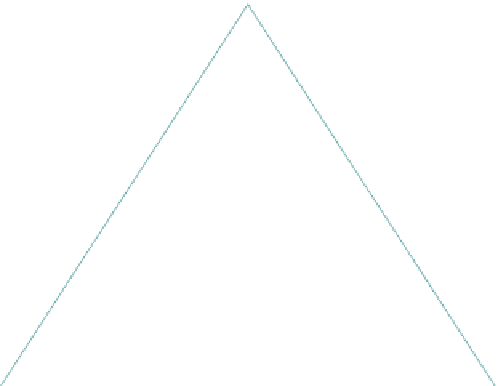
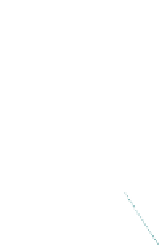
















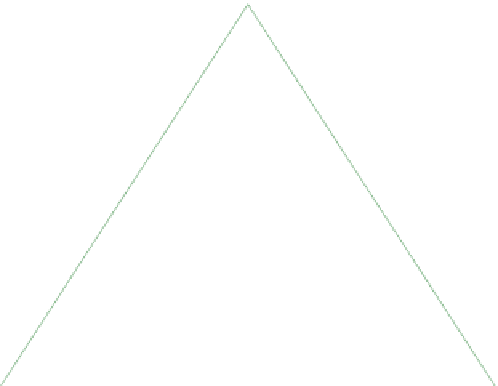
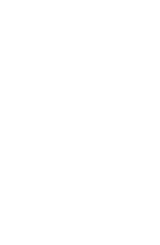

















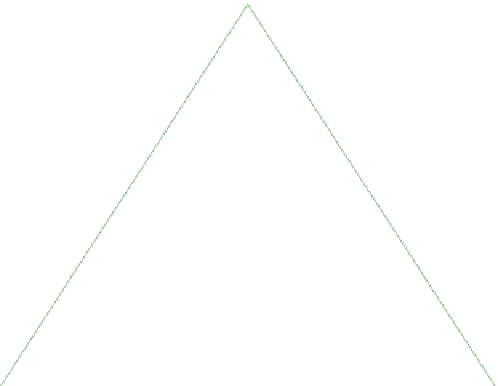


















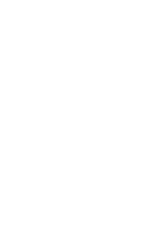






























































Search WWH ::

Custom Search