Environmental Engineering Reference
In-Depth Information
When grouting in rock in which the holes remain open and packers can be set, down-
stage grouting with packer would normally be adopted. However, in most chemical grout-
ing operations, either extremely weathered rock (i.e. virtually soil properties) or soil is being
grouted and it is necessary to support the hole from collapse and use different methods to
inject the grout.
Figure 18.28
shows the tube-à-manchette (“pipe with sleeves”) technique which is used
in Europe (and Australia) for grouting with chemicals.
In this technique the hole is drilled and cased to its full depth, the hole filled with a
cement/bentonite grout and the tube-à-manchette installed. This consists of a 40 mm to
60 mm diameter PVC tube, with 6 mm diameter boreholes in the wall of the tube at 300 mm
or 333 mm intervals. The holes are covered by a rubber sleeve.
Once installed, the casing is withdrawn and the grout allowed to 'set” to give a low
strength, relatively brittle grout.
The grouting operation is carried out by lowering a double packer to isolate one set of
outlet holes as shown in Figure 18.28, setting the packers, then applying the grout pres-
sure. The pressure of the grout lifts the rubber sleeve, fractures the bentonite-cement grout
and allows the chemical grout to penetrate into the soil or weathered rock.
Some idea of pre-grouting permeability can be obtained from the grout flow rate and
pressure but, as explained by Caron (1982), this may not be accurate because of unquan-
tifiable pressure losses through the fractures in the cement/bentonite grout.
Caron (1982) indicates that, when grouting in sands and gravels, practice differs from
country to country. In USA and Japan, grouting is commonly from the bottom of the cas-
ing used tosupport the hole, with the casing gradually withdrawn. For a two-shot grout,
such as sodium silicate/calcium chloride, the base grout (sodium silicate) is injected as the
casing is lowered and the reactant grout (calcium chloride) as the casing is withdrawn (as
shown in
Figure 18.29
)
.This method does allow checking of permeability before grout-
ing (but only crudely out of the bottom of the casing) and gives poorer control than the
tube-à-manchette system.
As shown in
Figure 18.30
, grouting should be carried out on a “closure” basis in depth
and plan and at least 3 lines of holes should be used to achieve this. Initial spacing should
be 2 to 3 times the anticipated final spacing.
18.4.4
Applications to dam engineering
Chemical grouts are expensive compared to cement or cement-bentonite grouts. As a
result, the use of chemical grouts will be restricted to those cases where seepage is critical
and not controllable by cement grouts or in cases of remedial works, particularly in allu-
vial (soil) foundations where cement grouts are not applicable.
As in the use of cement grouts, there is a limit to the permeability which can be achieved
by chemical grouting. Littlejohn (1985) suggests that practical minimum average perme-
abilities are:
10
7
m/sec in coarse sands and gravels (and only after “sophisticated chemicals, careful
injection procedures and close supervision”);
-
10
8
m/sec in “fissured” rock.
-
Since the grout curtain width is likely to be narrow (say 1 m to 1.5 m maximum per row
of holes), significant seepage reduction will result only when the original permeability is
relatively high compared to the grout curtain (see
Figure 18.13
).
Brett (1986) presents a plausible argument for two or three stage cement/bentonite, fol-
lowed by chemical grouting. The former is to fill the larger voids and hence reduce the
cost of chemicals.
Figure 18.31
illustrates this approach.
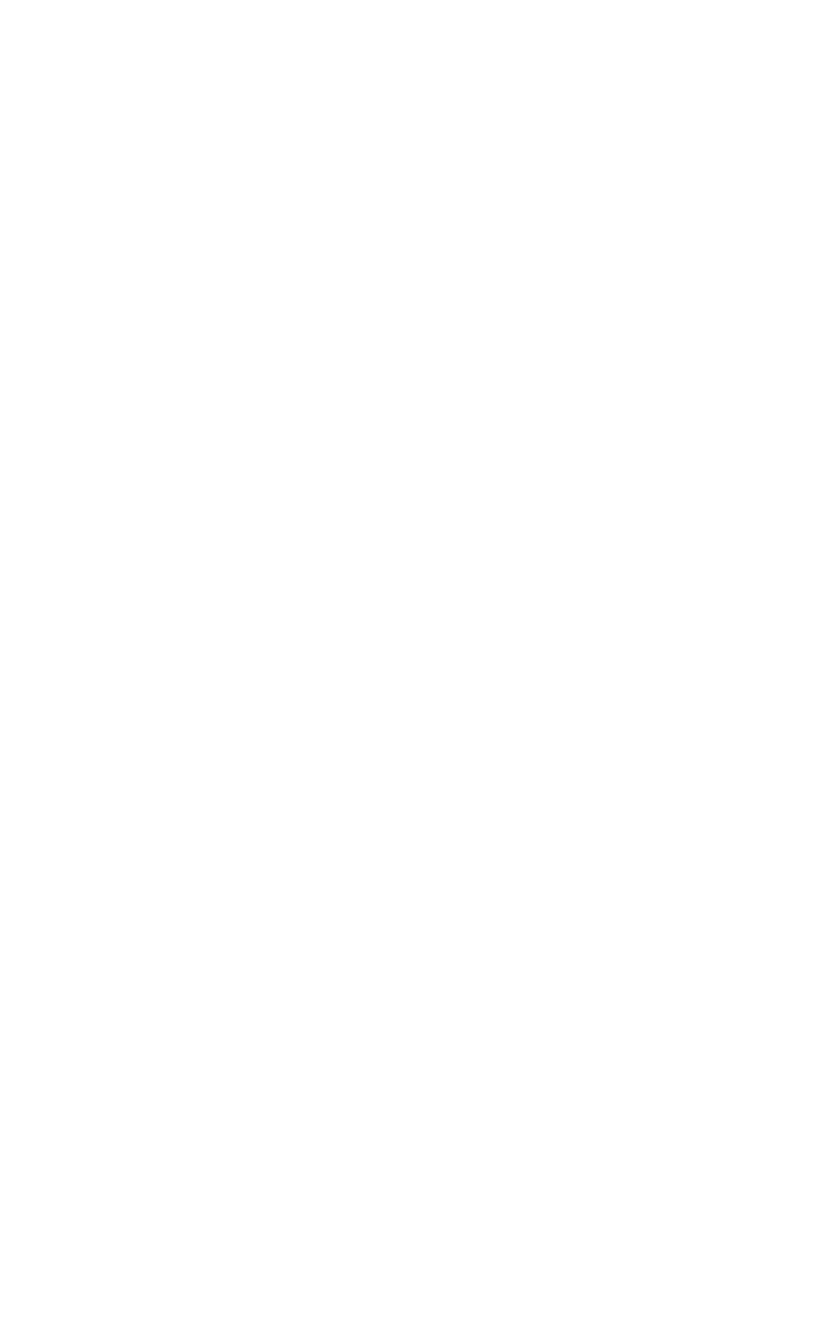